Orbital welding machine and traditional welding methods each offer unique advantages in the realm of metal joining and fabrication. This blog of Swisstech Schreiner delves into the core distinctions between orbital welding machines, known for their precision and consistency in challenging environments, and conventional welding techniques, celebrated for their versatility and accessibility. As we compare these methodologies, we'll highlight the technological advancements, application specifics, and skill requirements that make it different.
Overview of Welding Methods
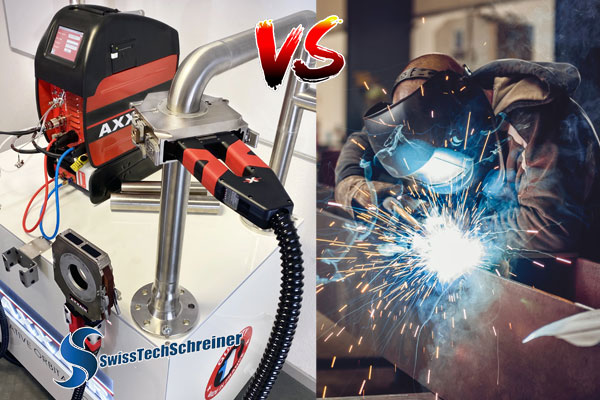
Orbital welding technology stands as a modern marvel in the world of metalwork, showcasing the pinnacle of precision and automation. In the construction industry, there are complex welding tasks, often prone to human error, orbital welding machines appear to instead the traditional welding. This cutting-edge technique, where the welding apparatus orbits around the stationary workpiece, ushers in unparalleled accuracy and consistency, especially in piping and tubing work where uniformity is paramount. But it's not just about the mechanics; the latest technology in orbital welding machines is nothing short of technological advancement. Sophisticated control systems that allow for meticulous adjustments, ensuring every weld is not just strong, but also aesthetically pleasing.
On the other hand, traditional welding methods like TIG, MIG, and Stick welding are the bedrock of the welding world. Each of these techniques, with their unique quirks and qualities, have sculpted the landscape of manufacturing for decades. TIG welding, with its finesse and precision, is like the paintbrush of an artist, perfect for delicate and intricate work. MIG welding, on the other hand, is the workhorse, favored for its speed and efficiency in handling a wide range of materials. Then there's Stick welding, the rugged, reliable old-timer, adaptable to almost any environment, even outdoors. These methods, while not as technologically advanced as orbital welding machine, offer flexibility and a human touch that machines can't replicate. They have their limitations, of course, like the requirement for skilled labor and the challenges with consistency.
Comparative Analysis of Orbital Welding Machines vs Traditional Welding Methods
The comparative analysis of orbital welding machines versus traditional welding methods reveals significant advancements in precision, efficiency, and automation, positioning orbital welding as a cutting-edge technology with distinct advantages in various industrial applications.
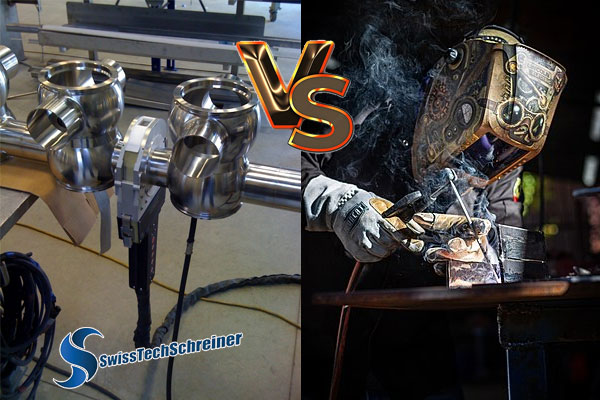
I. Efficiency and Productivity
The contrast between Orbital welding machines and traditional methods is striking, especially in terms of efficiency. Orbital welding stands out for its automated process, which significantly ramps up the speed, ensuring a consistent output rate. This automation is an important factor in industries where time, purity, and clean is money, such as the food and beverage industry and pharmaceuticals. In contrast, traditional methods, while reliable, often lag behind in speed due to their reliance on manual skills. The impact on productivity is clear: Orbital welding propels industries into a realm of heightened efficiency, making it a go-to for projects where time constraints are tight.
II. Precision and Quality of Welds
Precision is the vital factor when we compare the weld quality. Orbital welding, with its computer-controlled precision, ensures uniformity and perfection in every weld, a must-have in sectors where even a minor flaw can spell disaster. On the other hand, traditional welding methods, reliant on the artisan’s skill, can vary in quality. There are scenarios, particularly in custom or artistic work, where this human touch of traditional methods is irreplaceable. However, for industries where consistency is paramount, Orbital welding is the undisputed champion.
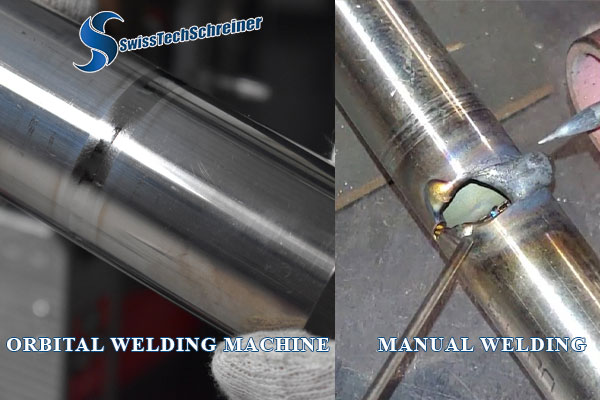
III. Cost and Investment
Talking about the financials, investments for each welding method is different. Orbital welding machines come with a hefty initial price tag, but they're getting better (and more cost-effective) over time, especially for large-scale operations. Traditional methods are more wallet-friendly initially but can become costlier in the long run due to lower efficiency and the need for skilled labor. For small-scale projects or businesses just starting, traditional welding might be the way to go. But for industrial giants, the initial investment in Orbital welding pays dividends in efficiency and consistency.
=> Read more at :
=>Components and Features of an Orbital Welding Machine
=>Reasons why orbital welding machines are suitable for pipe welding
=>The Advantages and Applications of Orbital Welding Machines in the Manufacturing Industry
IV. Ease of Use and Training
Ease of use and training are crucial in any industry. Traditional welding techniques have been around for ages, and while they require significant skill, they are well-understood and widely taught. Orbital welding is created to minimize costs, including training costs, saving years of training to become an expert welder. It demands a different skill set, more aligned with programming and machine operation. The learning curve might be required more, but once conquered, Orbital welding opens a world of efficiency and precision.
V. Safety and Environmental Impact
Safety and environmental considerations are paramount. Orbital welding, with its enclosed operation, minimizes risks and exposure to harmful elements, making it a safer option in many cases. Traditional methods, while effective, can pose higher safety risks due to direct human involvement. Environmentally, Orbital welding is a step ahead with its precise operation reducing waste and harmful emissions.
In conclusion, both Orbital welding machines and traditional welding have their place in the industrial landscape. The choice hinges on the specific needs of the project, balancing factors like cost, scale, quality, and environmental impact. It's not just about joining metals; it's about understanding the nuances of each method to make informed decisions. If your business is interested in orbital welding machine problems and solutions, please contact Swisstech Schreiner for advice and support.????️✨
Swisstech Schreiner.
Add: ch 4153 reinach and hcm city vietnam
Hotline: (+84) 931 - 386 - 062
Phone: (+84) 931 - 386 - 062 +84931386062 ( zalo / viber / whatsapp )
Email: swiss.tech.schreiner@gmail.com
Other News
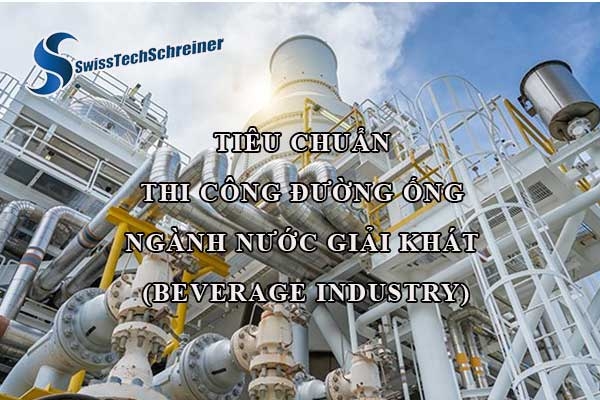
Tiêu chuẩn thi công đường ống ngành nước giải khát (beverage industry)
Swisstech Schreiner cung cấp tiêu chuẩn thi công đường ống ngành nước giải khát (beverage industry) hàng đầu đảm bảo chất lượng và hiệu suất tối ưu cho hệ thống. Tận dụng sự chuyên nghiệp và kinh nghiệm cam kết đem lại sự thành công và phát triển bền vững cho các doanh nghiệp trong ngành đồ uống.
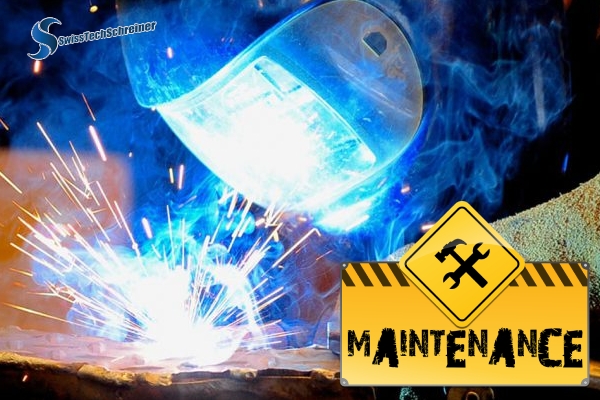
Quy trình bảo trì hàn (Maintenance work welding Process)
Trong quá trình sử dụng, các kết cấu hàn có thể bị hư hỏng hoặc xuống cấp do các yếu tố như thời tiết, tác động cơ học hoặc quá trình ăn mòn. Do đó, việc bảo trì hàn (Maintenance work welding) thường xuyên là rất cần thiết. Hãy cùng Swisstech Schreiner tìm hiểu quy trình bảo trì hàn qua bài viết sau.
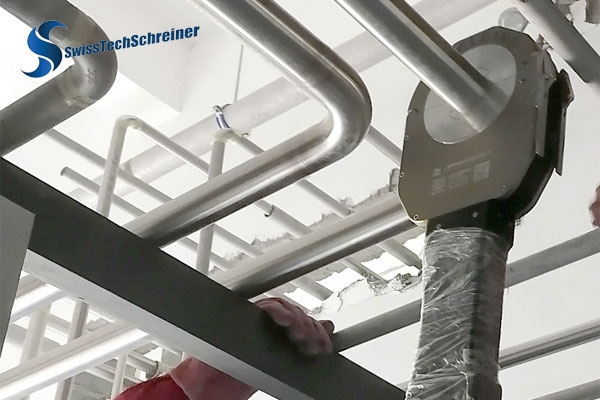
Precision and Durability Stainless Steel Pipe Processing
People often laud stainless steel for its strength, corrosion resistance, and aesthetic appeal. A significant facet of this material's utility lies in its transformation into pipes. Let's have Swisstech Schreiner delve into the world of stainless steel pipe processing.
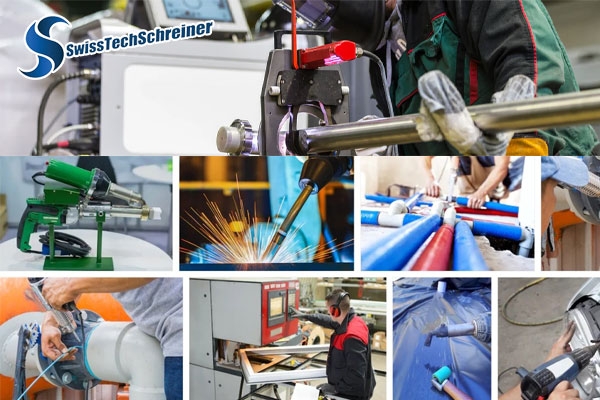
Công nghệ Hàn orbital giúp đảm bảo an toàn thực phẩm
Công nghệ hàn quỹ đạo Orbital welding technology đã và đang trở thành một giải pháp hàng đầu, giúp nâng cao tiêu chuẩn an toàn thực phẩm. Hãy cùng Swisstech Schreiner tìm hiểu về công nghệ hàn orbital và tác động tích cực của nó đối với ngành công nghiệp thực phẩm hiện đại.
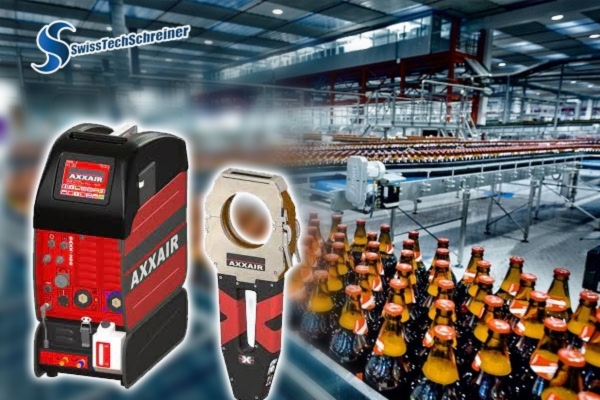
SwissTech Schreiner – Hàn Quỹ Đạo Tối Ưu Cho Ngành Nước Giải Khát
Trong các dây chuyền sản xuất nước giải khát, hệ thống ống dẫn đóng vai trò quan trọng trong việc vận chuyển nguyên liệu và sản phẩm. Việc sử dụng ống thép không gỉ vi sinh cùng công nghệ hàn quỹ đạo là lựa chọn tối ưu để đảm bảo
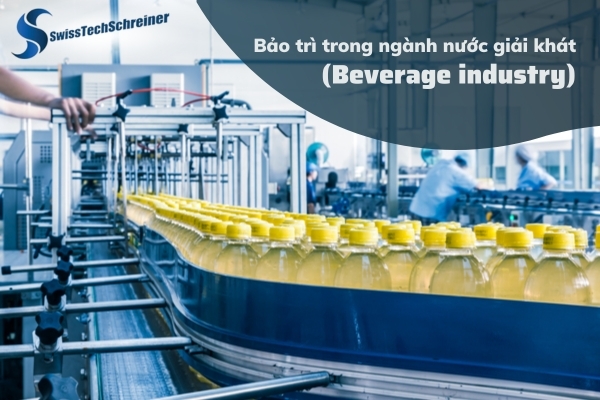
Bảo trì trong ngành nước giải khát (Beverage industry)
Bảo trì là một hoạt động không thể thiếu trong ngành nước giải khát, vì nó ảnh hưởng trực tiếp đến chất lượng và an toàn của các sản phẩm dành cho người tiêu dùng. Tuy nhiên, việc bảo trì cũng gặp phải nhiều khó khăn và thách thức do các yêu cầu quy định nghiêm ngặt, các thiết bị sản xuất phức tạp. Trong bài viết này Swisstech Schreiner sẽ chia sẻ tầm quan trọng trong công việc bảo trì (Maintenance work) và quy trình bảo trì cho ngành nước giải khát (Beverage industry) hiệu quả nhất nhé.