Orbital welding machines represent a specialized segment of welding equipment designed to provide high-quality and consistent welds, particularly in environments where precision and repeatability are paramount. This article from Swisstech Schreiner writes about the features, applications, and technological advancements of orbital welding machines, illustrating their importance in various industrial sectors.
Introduction to Orbital Welding Technology
Orbital welding is an automated welding process that utilizes specialized equipment to rotate the welding arc around a stationary workpiece, typically a pipe or tube. This method contrasts with traditional welding, where the workpiece or the welding torch is manually manipulated. The automation in orbital welding technology ensures high precision and repeatability, essential in industries where weld integrity is critical.
Components of an Orbital Welding Machine
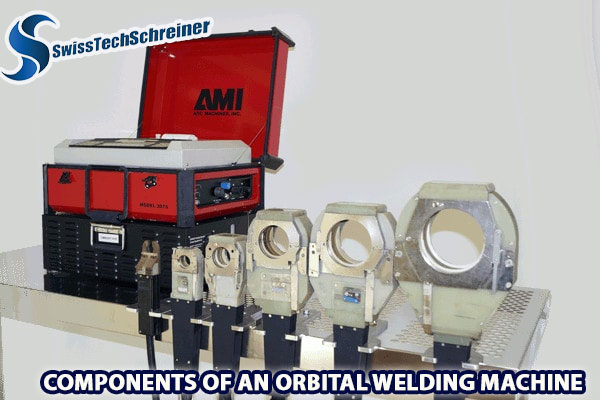
Power Supply: The power supply unit controls the welding parameters like current, voltage, and welding speed.
Weld Head: This component holds and rotates the welding torch around the workpiece.
Control System: A sophisticated control system, often with a programmable interface, allows for precise adjustments of welding parameters.
Wire Feed Mechanism: In some orbital welding systems, a mechanism feeds the welding wire automatically.
This advanced feature seamlessly feeds the welding wire into the weld pool, ensuring a steady and uninterrupted welding process, thus enhancing both the efficiency and the integrity of the welds. Together, these components form the backbone of orbital welding machines, embodying technological sophistication and offering unparalleled precision in critical welding operations.
Applications of Orbital Welding Technology
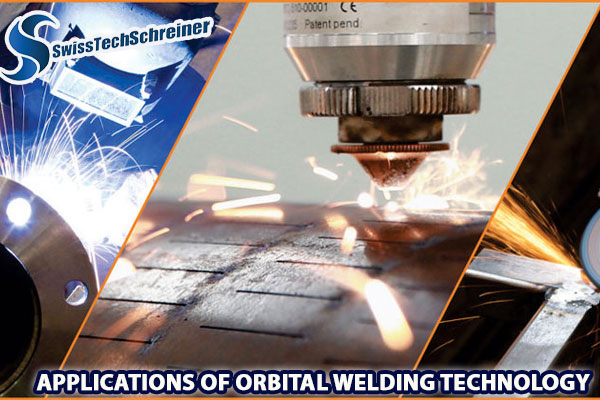
Orbital welding machines have carved a niche in various industries, becoming an indispensable tool wherever the utmost quality in pipe and tubing welds is demanded. In the aerospace sector, these machines play a pivotal role, delivering precision welds essential for aircraft components and fuel lines, where the slightest flaw can have significant consequences. The pharmaceutical industry, too, relies on orbital welding pharmaceutical creating sterile piping systems, ensuring the purity and safety of medical products. Similarly, in semiconductor manufacturing, orbital welding is crucial for assembling ultra-high-purity systems, a testament to its ability to maintain the highest standards of cleanliness and precision.
The robustness of orbital welding also extends to the demanding environments of the oil and gas industry, where it is employed in both onshore and offshore pipeline welding, a testimony to its versatility and reliability. Furthermore, the food and beverage industry, orbital welding is the method of choice for constructing critical piping systems, underlining its importance in sectors where safety and precision are paramount. This widespread application across diverse and critical industries underscores the versatility and reliability of orbital tig welding machines, making them a cornerstone in modern industrial operations.
Advantages of Orbital Welding Machine
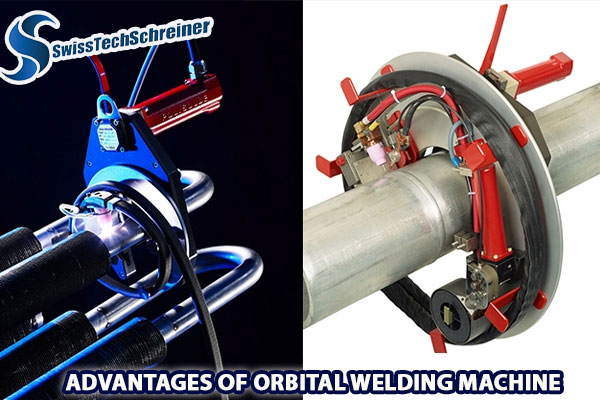
Orbital welding machine stands out in the welding landscape for its exceptional blend of benefits, primarily driven by its automation capabilities. This technology shines in delivering consistent quality, as its automated controls are finely tuned to produce uniform welds with remarkable precision, a feature that’s crucial in applications demanding high standards. The automation aspect also significantly diminishes the likelihood of human error, a vital factor in maintaining the integrity of welds.
Moreover, this mechanized approach contributes to enhanced efficiency, outpacing manual welding in terms of speed and reducing the overall time taken for projects. Orbital welding's adaptability is another feather in its cap, capable of handling a diverse range of materials and accommodating various pipe diameters, making it a versatile tool in a welder's arsenal.
Additionally, a pivotal advantage of orbital welding technology is the heightened safety it offers. By reducing the welder's direct exposure to potentially hazardous conditions, orbital welding not only ensures the safety of the personnel but also contributes to a safer work environment. This amalgamation of consistent quality, reduced error, efficiency, flexibility, and safety makes orbital welding a highly sought-after solution in industries where welding is a critical component of operations.
Technological Advancements
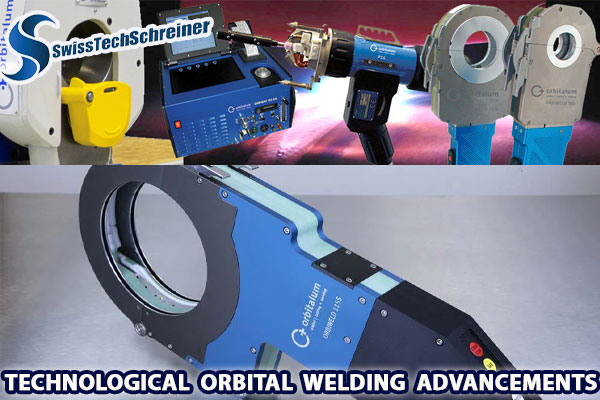
The landscape of orbital welding technology has been revolutionized by a series of recent advancements, marking a significant leap forward in its capabilities and applications. A key development is the integration with digital systems, which has transformed the way welding operations are monitored and controlled. By harnessing digital interfaces, operators can now enjoy enhanced oversight and precision in their welding tasks, making the process more efficient and reliable. Complementing this technological stride is the evolution of welding heads. These have become more compact and versatile, broadening the scope of their application and allowing them to adapt to a variety of welding scenarios with ease.
Furthermore, the leap in programming capabilities stands out as a monumental advancement. Modern automatic orbital welding machines are now equipped to handle complex weld patterns and intricate parameter adjustments, providing an unprecedented level of control over the welding process. Additionally, the advancements in remote operation capabilities have opened new frontiers, particularly in executing welding tasks in environments that are hazardous or difficult to access.
This not only enhances safety but also extends the utility of orbital welding technology to previously challenging locales. Collectively, these innovations have not only elevated the efficiency and scope of orbital welding but have also positioned it as a cutting-edge tool in the welding industry, ready to meet the ever-evolving demands of modern manufacturing and construction projects.
=> See more articles on the same topic at :
=> Reasons why orbital welding machines are suitable for pipe welding
=> Choosing the right pipe welding method?- Orbital welding machine
Challenges and Future Trends
While orbital welding machines offer numerous advantages, they also present challenges such as the high initial investment and the need for skilled operators to program and maintain the machines. Future trends in orbital welding technology may include greater automation, integration with artificial intelligence for adaptive welding processes, and further miniaturization of equipment.
Conclusion
Orbital welding machines have revolutionized welding in industries where precision and consistency are non-negotiable. As technology continues to evolve, these machines are set to become even more integral in various industrial processes, offering solutions that combine efficiency, quality, and safety. Contact Swisstech Schreiner if your business needs any information or solutions about orbital welding technology, equipment, orbital welding machines, orbital welding stainless steel pipe, installation and construction of industrial pipeline systems,...
Swisstech Schreiner.
Add: ch 4153 reinach and hcm city vietnam
Hotline: (+84) 931 - 386 - 062
Phone: (+84) 931 - 386 - 062 +84931386062 ( zalo / viber / whatsapp )
Email: swiss.tech.schreiner@gmail.com
Other News
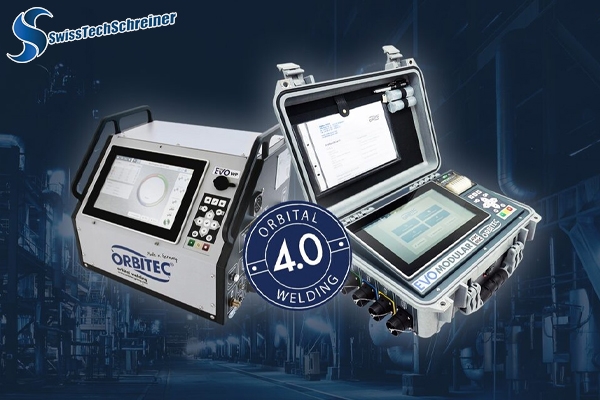
Công nghệ hàn quỹ đạo (orbital welding technology) được thực hiện như thế nào?
Công nghệ hàn quỹ đạo (orbital welding technology) đã trở thành một công cụ quan trọng trong các lĩnh vực như hàng không vũ trụ, công nghiệp chế tạo, năng lượng tái tạo, ngành dược phẩm và ngành nước giải khát. Hãy theo dõi bài viết sau của Swisstech Schreiner để tìm hiểu công nghệ hàn quỹ đạo (orbital welding technology) được thực hiện như thế nào và những lợi ích khi ứng dụng nó nhé.
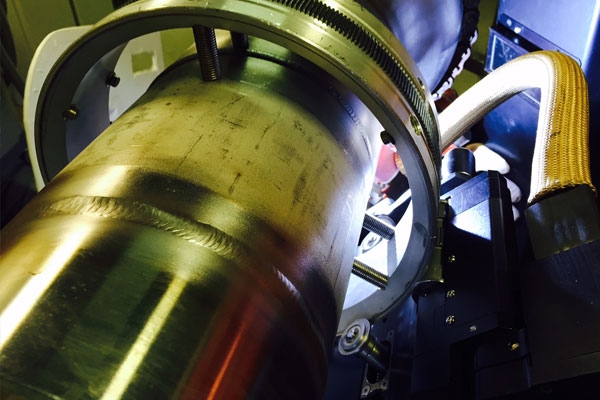
The stainless steel pipe processing
Swisstech Schreiner is always proud to be the leader in the field of stainless steel pipe processing with a team of experienced employees. We offer solutions about the stainless steel pipe processing for pipeline systems and services related to maintenance work and orbital welding technology.
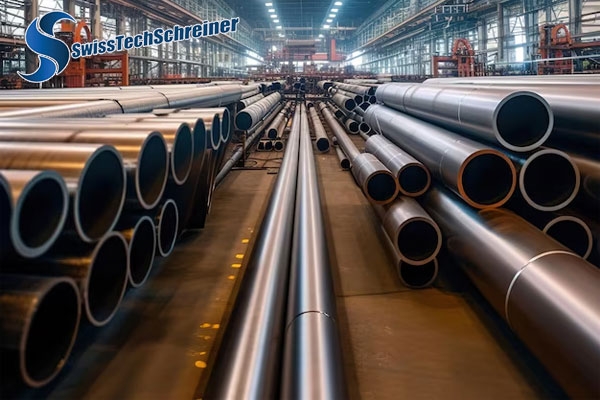
Các lỗi mối hàn xấu và cách khắc phục nhanh chóng, hiệu quả
Khám phá các lỗi mối hàn xấu thường gặp và cách khắc phục nhanh chóng, hiệu quả. Đảm bảo chất lượng, độ bền khi gia công ống thép không gỉ Stainless steel pipe processing cho các công trình và an toàn trong sản xuất cùng Swisstech Schreiner.
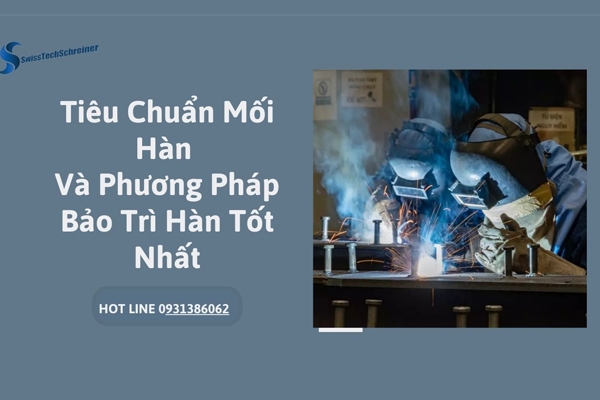
Tiêu Chuẩn Mối Hàn Và Phương Pháp Bảo Trì Hàn Tốt Nhất
Kiểm tra mối hàn để đánh giá chất lượng là điều vô cùng quan trọng không thể bỏ qua. Điều này nhằm đảm bảo về thẩm mỹ, chất lượng của mối hàn đẹp, bền, chắc chắn,.. Bên cạnh đó, việc sửa chữa, nâng cấp và bảo trì hàn (Maintenance work welding) cũng được hạn chế.
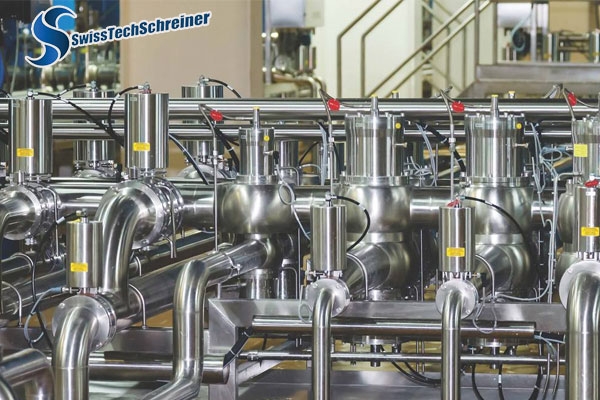
The Orbital Welding Technology in the Beverage Industry: Revolutionizing Quality and Efficiency
Discover how orbital welding technology is transforming the beverage industry, revolutionizing production quality and efficiency. Let's at Swisstech Schreiner explore the techniques and innovations that are raising the bar for beverage manufacturing in this exploration of orbital welding's impact.
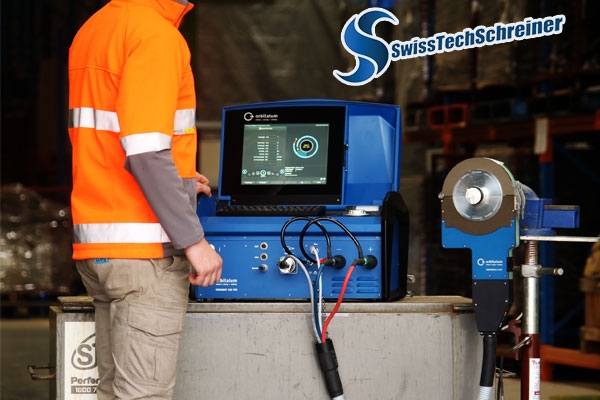
How to Use Orbital Welding Technology Properly: A Comprehensive Guide
Orbital welding technology, when done with the right techniques and attention to detail, can produce welds that are a perfect blend of strength and beauty. Embrace these techniques shared by Swisstech Schreiner, and let your welds be the benchmark of excellence.