Orbital welding technology, a specialized arena in the world of welding, offers precision and repeatability in applications where standard welding processes fall short. In industries like aerospace, semiconductor, and pharmaceutical, where tube and pipe welding require utmost accuracy, orbital welding reigns supreme. If you're considering integrating this technology or improving your existing processes, read on the following article by Swisstech Schreiner to understand how to use orbital welding technology properly.
Orbital welding technology in industries
Orbital welding technology is an automated welding process that utilizes a tungsten electrode rotating (or orbiting) around a stationary workpiece, typically a tube or pipe. This automation ensures uniform welds, reduces the chances of errors, and can lead to higher production rates compared to manual welding.
Steps to Use Orbital Welding Technology Properly
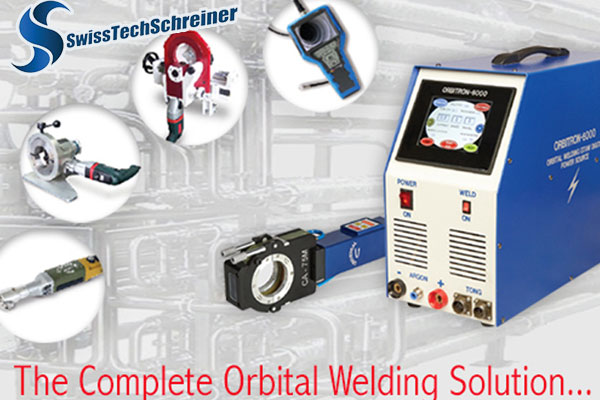
Choosing the Right Tools and Setup for Orbital Welding:
When setting up for orbital welding, it's crucial to pick tools and components tailored to your specific task. Start by opting for a power supply that aligns with the requirements of your orbital welding job. Next, based on the tubes' or pipes' diameter and thickness, select a weld head that's a perfect fit. Don't forget about the shielding gas; always go for high-purity variants, and fine-tune the flow rate for optimum results.
The Importance of Preparation:
Before diving into orbital welding technology, prepping your materials can make all the difference. The welding zone should be free from any impurities. So, whether it's by manual scrubbing, using chemical agents, or employing a mix of both, ensure your materials are pristine. Additionally, precise alignment is vital. Any discrepancies in positioning can lead to defects, so always double-check that your tubes or pipes are correctly set in their fixture.
Configuring Your Weld Settings:
Setting up your weld parameters requires a thorough understanding of your material. Factors like its thickness dictate the amperage, voltage, and travel speed. If in doubt, the equipment's user guide or a seasoned welding engineer can offer invaluable insights. Contemporary orbital welding equipment comes equipped with multi-segment programming capabilities, offering enhanced control over the welding procedure. It's also a good practice to conduct test welds on excess material before the main operation, ensuring that your chosen settings are spot on.
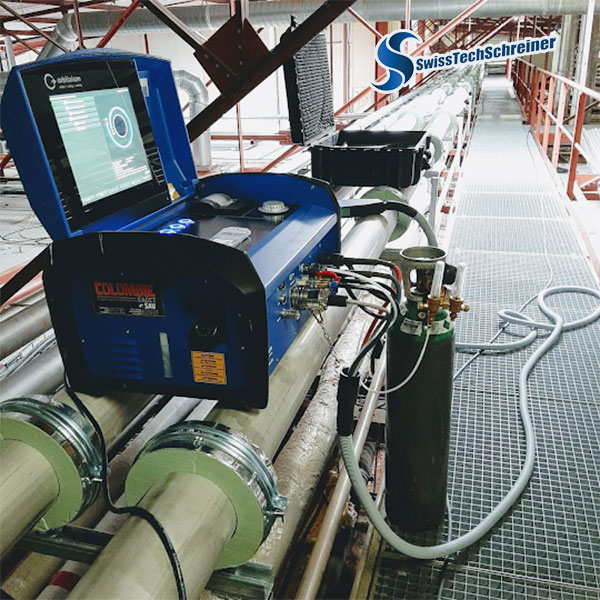
Maintenance and Quality Assurance:
For the longevity and efficiency of your orbital welding machine, regular upkeep is non-negotiable. This includes cleaning the weld head, replacing parts showing wear and tear, and ensuring the tungsten electrode is not only sharp but also perfectly centered.
But, it's not just about the tools; the end product's quality is paramount. Therefore, always document the parameters used for every weld. This meticulous record-keeping is indispensable, especially in sectors where every step needs accounting for. And, to be doubly sure of your weld's quality, utilize non-destructive evaluation methods like X-ray or ultrasonic tests.
=> See more articles on the same topic at:
=> Application of Orbital Welding Technology in the Construction of Industrial Pipeline Systems
=> The reason for using an Orbital Welding technology
=> The Orbital Welding Technology in the Beverage Industry: Revolutionizing Quality and Efficiency
Mastering the Art of Orbital Welding for Flawless Results
Orbital welding technology, with its advanced technology and precise techniques, can produce welds that are not only structurally sound but also aesthetically pleasing. For those looking to achieve beautiful welds using orbital welding machines, certain methodologies can make all the difference.
Prioritize Surface Preparation:
The canvas for your welding art is the surface of the materials you're joining. Just as an artist wouldn’t paint on a dirty canvas, welders shouldn't work on unprepared surfaces. Dedicate time to thorough cleaning, ensuring the removal of any oxides, contaminants, or residues. The cleaner the metal, the smoother and more appealing the weld bead will appear.
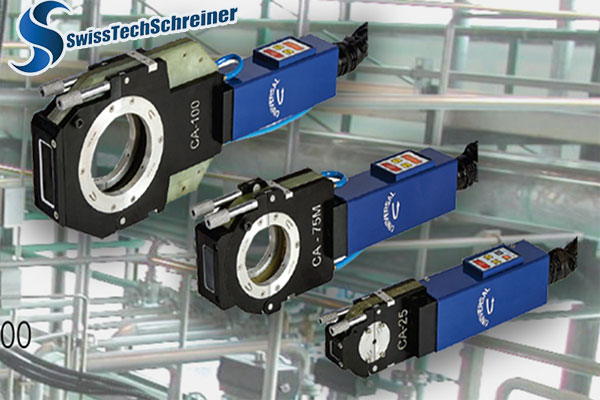
Utilize Pulse Welding:
Pulse welding is a game-changer for achieving neat welds. By controlling the heat input and allowing cooler periods between pulses, you get a more controlled weld pool. The result? Uniform and beautiful ripple patterns that are a hallmark of top-tier welding work.
Consistent Travel Speed:
A steady hand ensures a consistent travel speed, leading to an even bead without over-penetration or undercutting. For a weld that looks as good as it holds, maintaining an unwavering speed is essential. Many modern orbital welding machines come with features that help regulate this, so be sure to leverage them.
Optimize Gas Shielding:
A proper shielding gas flow ensures protection from atmospheric contaminants. By selecting the right type and ensuring its consistent flow, you can prevent discoloration and achieve that shiny, silver finish on your welds.
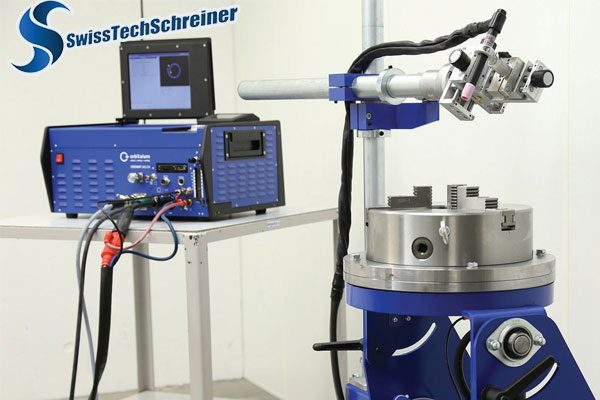
Post-Weld Polishing:
For welds that truly shine, consider a post-weld polishing or passivation process. This not only enhances the weld's appearance but also helps in preventing corrosion, especially for stainless steel.
Regular Equipment Checks:
Remember, even the best techniques can falter with sub-par equipment. Regularly inspect and maintain your orbital welding machine. A well-maintained machine ensures consistent energy output and precise control, both critical for beautiful welds.
Orbital welding technology, when done with the right techniques and attention to detail, can produce welds that are a perfect blend of strength and beauty. As the world of welding evolves, blending art with science can set you apart. Embrace these techniques shared by Swisstech Schreiner, and let your welds be the benchmark of excellence.
Remember, like any technology, the key to success with orbital welding technology is a combination of the right equipment, proper training, and consistent practice.
Swisstech Schreiner.
Add: ch 4153 reinach and hcm city vietnam
Hotline: (+84) 931 - 386 - 062
Phone: (+84) 931 - 386 - 062 +84931386062 ( zalo / viber / whatsapp )
Email: swiss.tech.schreiner@gmail.com
Other News
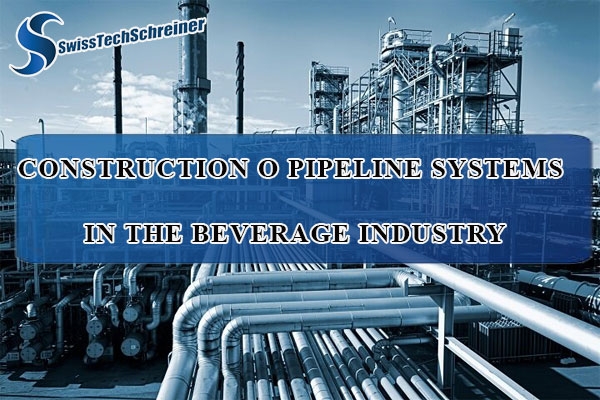
Construction of pipeline systems in the beverage industry
Let's Swisstech Schreiner discover the intricate process behind constructing efficient pipeline systems tailored for the dynamic demands of the beverage industry. Explore key techniques (orbital welding machine), and considerations for ensuring seamless liquid transport, hygiene, and quality.
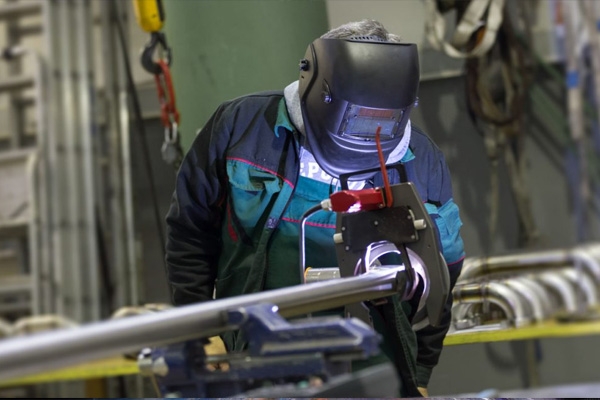
Ứng dụng máy hàn quỹ đạo (Orbital welding machine) vào công nghiệp
Công nghệ Hàn quỹ đạo - Orbital welding technology là công nghệ ứng dụng hàn tự động các loại ống thép không gỉ trong các xí nghiệp, nhà máy được bảo vệ trong các điều kiện sạch sẽ. Đây là công nghệ được các ngành công nghiệp ưa chuộng nhất hiện nay.
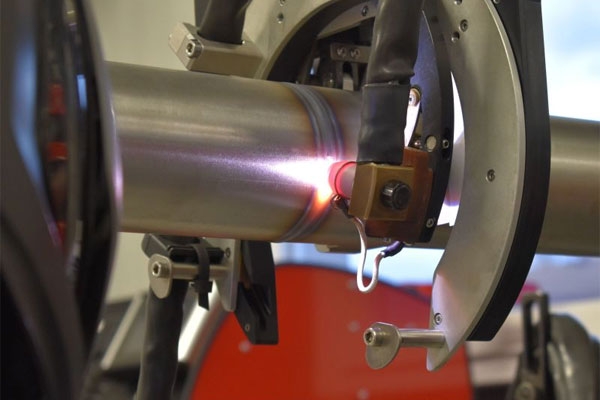
Ứng dụng và lợi ích của máy hàn quỹ đạo trong kỹ thuật đường ống
Tìm hiểu ứng dụng và lợi ích của máy hàn quỹ đạo Orbital welding machine trong kỹ thuật đường ống. Khám phá nguyên lý hoạt động, ưu điểm vượt trội và các ứng dụng thực tiễn trong lắp đặt, bảo trì và chế tạo đường ống cho các ngành thực phẩm, đồ uống, dược phẩm.
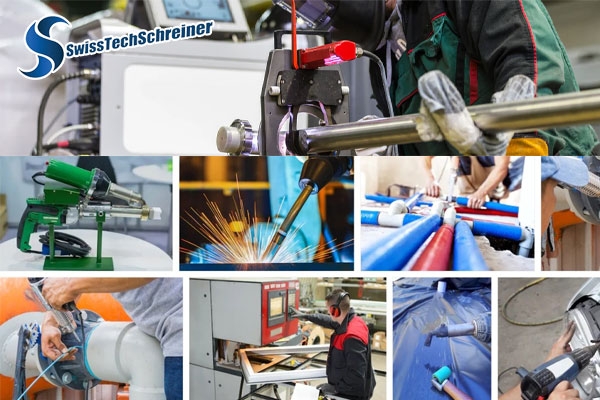
Công nghệ Hàn orbital giúp đảm bảo an toàn thực phẩm
Công nghệ hàn quỹ đạo Orbital welding technology đã và đang trở thành một giải pháp hàng đầu, giúp nâng cao tiêu chuẩn an toàn thực phẩm. Hãy cùng Swisstech Schreiner tìm hiểu về công nghệ hàn orbital và tác động tích cực của nó đối với ngành công nghiệp thực phẩm hiện đại.
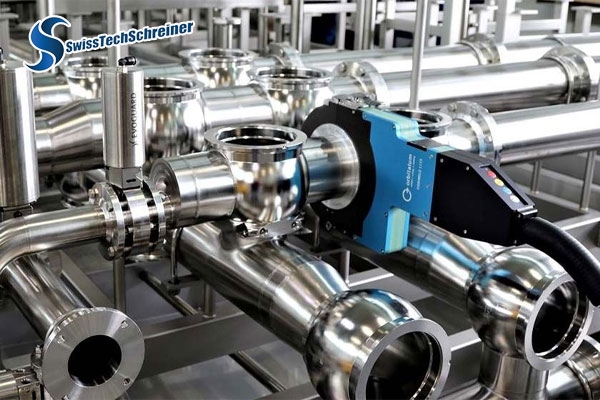
Công Nghệ Hàn Quỹ Đạo: 3 Lợi Ích Nổi Bật Và Ứng Dụng Thực Tiễn
Nếu bạn đang tìm kiếm một giải pháp hàn vượt trội, hãy cân nhắc công nghệ hàn quỹ đạo Orbital welding technology của Swisstech Schreiner để đảm bảo mối hàn chất lượng cao, bền bỉ và đáng tin cậy cho sản phẩm của bạn.
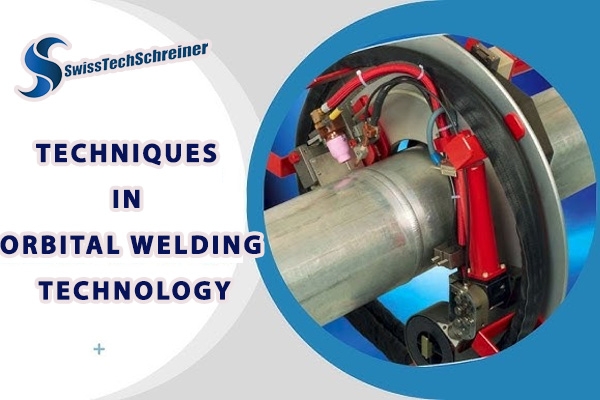
Different Techniques In Orbital Welding Technology
Orbital welding technology stands at the forefront of precision and efficiency in the welding industry. Join Swisstech Schreiner uncovering the various techniques that have revolutionized pipeline construction, food and beverage industry, and numerous other sectors requiring impeccable welds.