In the world of industrial pipeline systems, precision and reliability are paramount. Traditionally, the welding of pipes was done manually, which, while effective, presented challenges in terms of consistency and speed. Enter orbital welding technology in the construction and maintenance of industrial pipeline systems. This innovation has not only enhanced efficiency but has also offered a slew of benefits in terms of quality, safety, and cost-effectiveness. Let's Swisstech Schreiner delve into the fascinating realm of orbital welding and its transformative impact on pipeline construction.
Effectiveness of Orbital Welding Technology
Orbital welding technology is an automated welding process where the torch rotates mechanically around a stationary workpiece, typically a pipe or tube. The primary advantage? It provides uniform welds, minimizing human error and ensuring an impeccable weld seam. This technology originated in the aerospace industry, where precision was non-negotiable, and has since found its home in numerous industrial applications. At its core, this technology employs a combination of advanced computer controls and specialized machinery, ensuring that each weld is executed with pinpoint precision.
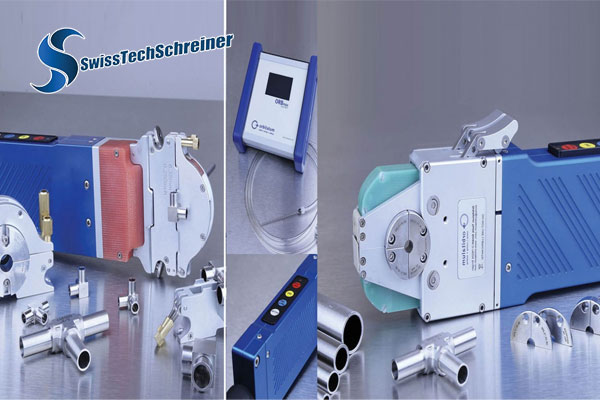
Enhanced Quality and Consistency
One of the standout advantages of orbital welding technology is its ability to produce high-quality welds with unparalleled consistency. Unlike manual welding, where skill levels might vary from one welder to another, orbital welding offers repeatability. This is particularly crucial for industries where the smallest imperfection can lead to catastrophic failures, such as in the chemical, pharmaceutical, food and beverage industry or nuclear sectors. The mechanized process ensures that every weld meets the desired standards, reducing the risk of leaks or breaches. The resultant pipelines boast enhanced durability, fewer defects, and a significantly reduced susceptibility to leaks. This, in turn, translates to safer operations, minimized maintenance interventions, and prolonged system lifespans.
Efficiency and Speed
Time is often of the essence in industrial settings. Orbital welding technology, being automated, drastically reduces the time required to complete a welding job. It's especially beneficial for large projects with hundreds or even thousands of weld joints. With its swift operation, projects can be completed faster, leading to reduced downtime and quicker time-to-market for many products.
This technology leverages advanced computer systems and precision machinery, allowing for unparalleled accuracy, reduced wastage, and optimal strength in the resultant joints. The result is a robust pipeline network that stands up to the rigorous demands of industrial applications, reducing maintenance costs and enhancing the overall operational efficiency.
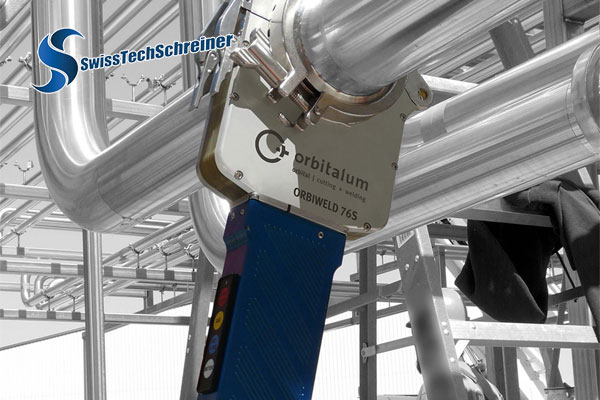
=> Read more : Orbital Welding Technology Standards in the Beverage Industry
Safety and Worker Well-being
Traditional manual welding, especially in confined spaces or challenging environments, can pose risks to workers. With the introduction of orbital welding, the need for welders to operate in such conditions diminishes. The technology allows for remote operation, ensuring that workers are kept at a safe distance from potential hazards. This not only enhances worker safety but also contributes to overall project safety by reducing the chances of accidents or mishaps.
Moreover, orbital welding technology with the surge in industries aiming for higher standards of safety and reliability, the adoption of orbital welding has been pivotal. Not only does it ensure a seamless construction process, but it also resonates with industry professionals who recognize its superior quality assurance. Industries worldwide are taking note, and as they continue to prioritize safety, efficiency, and cost-effectiveness, the prominence of orbital welding is only set to grow.
Orbital welding technology, often hailed as a revolution in the construction of industrial pipeline systems, has reshaped the way industries approach the intricate process of pipe assembly. Unlike traditional welding methods that are heavily reliant on the skill of the welder, orbital welding is an automated system that ensures consistent, high-quality welds, even in challenging environments or tight spaces.
=> Read more at : The reason for using an Orbital Welding technology
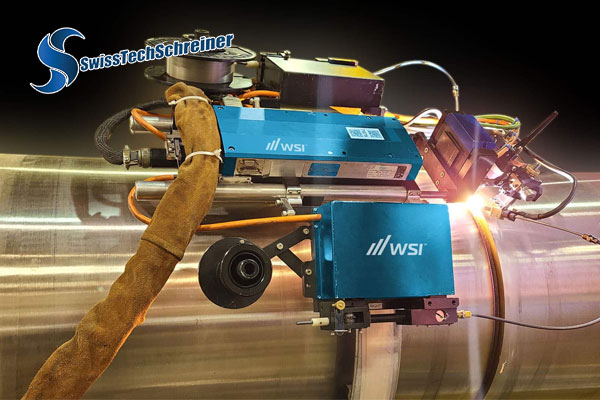
Cost-Effectiveness in the Long Run
While the initial investment in orbital welding equipment might seem substantial, the long-term benefits often outweigh the costs. Given the speed, efficiency, and reduced need for rework due to fewer errors, projects can often be completed under budget. Moreover, the durability and reliability of the welds mean that maintenance costs over the pipeline's lifecycle are significantly reduced.
Orbital welding technology has revolutionized the way industrial pipeline systems are constructed. Its application ensures top-notch quality, safety, and efficiency, making it an invaluable tool for industries worldwide. As we continue to see advancements in this technology, one can only imagine the heights it will reach in further optimizing and simplifying the intricate world of industrial pipeline construction. Whether you're an industry professional or merely a tech enthusiast, the marvels of orbital welding are sure to captivate your interest. It is no longer just a novel approach but is fast becoming the gold standard in industrial pipeline construction.
Swisstech Schreiner.
Add: ch 4153 reinach and hcm city vietnam
Hotline: (+84) 931 - 386 - 062
Phone: (+84) 931 - 386 - 062 +84931386062 ( zalo / viber / whatsapp )
Email: swiss.tech.schreiner@gmail.com
Other News
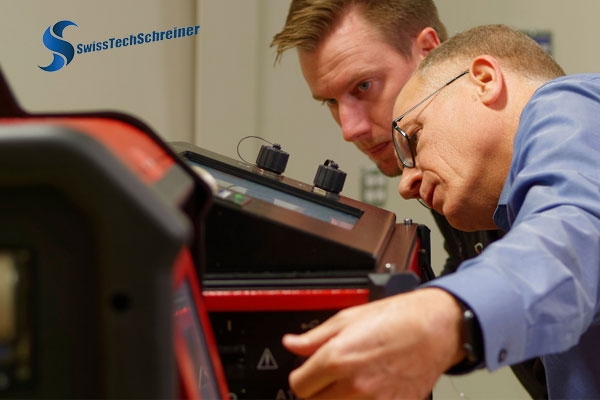
Maintenance Work Welding for Ultimate Durability and Lifetime
In this article, we'll explore the reasons for regular maintenance of orbital welding machines and provide practical tips on how to properly care for them. At SwissTech Schreiner, we offer top-notch maintenance work welding services to keep your machines in peak condition and reliable performance.
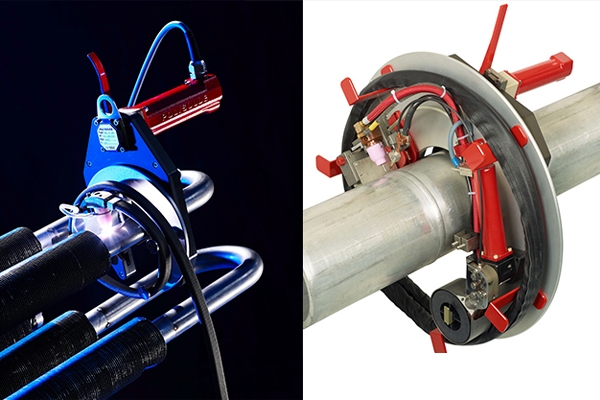
Cấu tạo của máy hàn quỹ đạo (orbital welding machine) và cách hoạt động
Máy hàn quỹ đạo (orbital welding machine) là gì? Cấu tạo và cách thức hoạt động của máy là như thể nào? Hãy cùng Swisstech Schreiner tìm hiểu chi tiết về máy hàn quỹ đạo (orbital welding machine) ở bài viết dưới đây nhé.
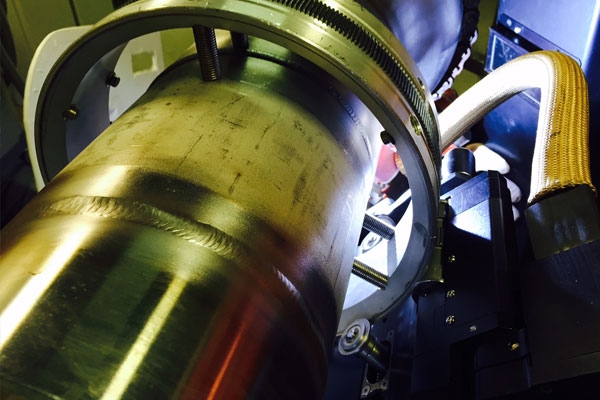
The stainless steel pipe processing
Swisstech Schreiner is always proud to be the leader in the field of stainless steel pipe processing with a team of experienced employees. We offer solutions about the stainless steel pipe processing for pipeline systems and services related to maintenance work and orbital welding technology.
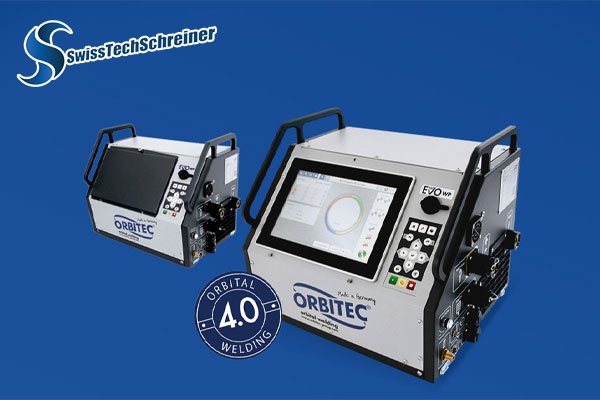
Công nghệ hàn quỹ đạo Orbital welding technology và Ứng dụng trong Hệ thống Ống dẫn Đồ uống
Khám phá công nghệ hàn quỹ đạo Orbital welding technology trong ngành công nghiệp đồ uống: đảm bảo chất lượng mối hàn, đơn giản hóa quá trình vận hành và tăng hiệu quả không gian làm việc. Tìm hiểu lợi ích và ROI ấn tượng chỉ sau 12 tháng đầu tư.
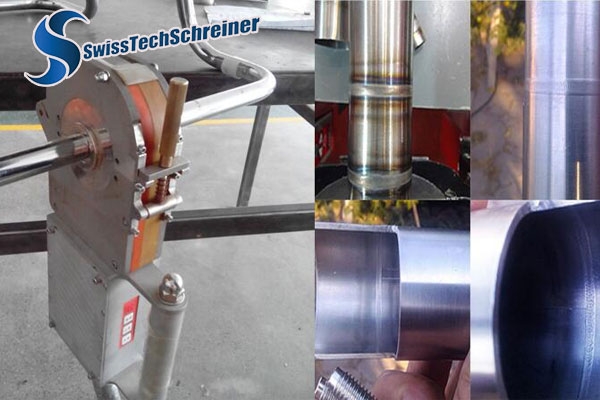
Services related to Orbital Welding Machine
If you are considering purchasing an orbital welding machine or hire services related to orbital welding, there are several factors to consider to ensure that you make the right investment. Swiss Tech Schreiner will discuss everything you need to know about orbital welding machines in this blog.
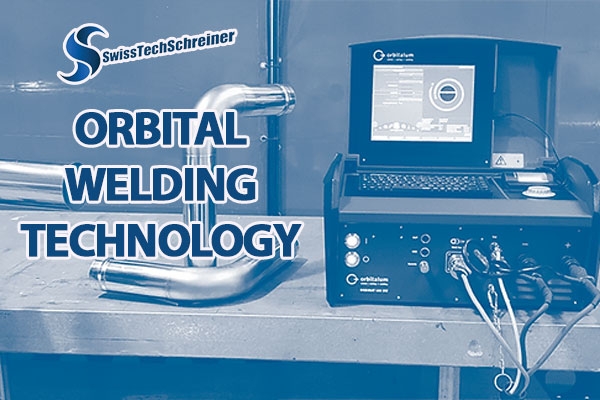
Orbital Welding technology - automatic welding machine service
Do you need to rent, buy, train or modify an orbital welding machine or orbital welding technology services ? Contact our hotline: (+84) 931 - 386 - 062 or swiss.tech.schreiner@gmail.com for detailed information. Or you can fill out the form below to let Swisstech Schreiner know your request.