The beverage industry is much more than the refreshing drink production that you sip on. Behind that invigorating taste is an intricate network of processing, manufacturing, and delivery mechanisms that must be impeccable in their operation. Among these mechanisms, the role played by welding, particularly orbital welding, is pivotal. If you've ever wondered about the rigorous standards behind the drinks you consume, let's Swisstech Schreiner dive deep into the significance of orbital welding technology standards in the beverage sector.
What is Orbital Welding Technology?
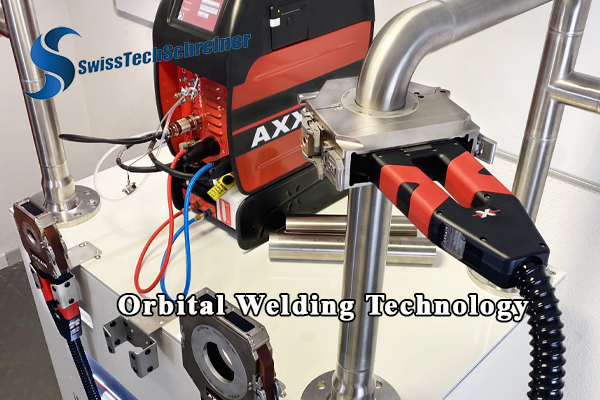
Orbital welding technology is an automated welding technique that utilizes specialized equipment to rotate the welding arc around a stationary workpiece, most often tubes or pipes. This ensures a uniform, high-quality weld that is consistent, reliable, and free from potential contaminants or inconsistencies.
Why is Orbital Welding Technology Preferred in the Beverage Industry?
Sanitary Standards: The beverage industry is one governed by strict sanitary guidelines. Contaminants can have dire consequences, from affecting taste to introducing health risks. Traditional welding methods can result in irregularities or crevices in pipes where bacteria can thrive. Orbital welding technology, on the other hand, creates smooth, consistent, and crevice-free welds, making them resistant to bacterial growth.
Reliability: Orbital welding technology is an automated process, eliminating the inconsistencies associated with manual welding. This guarantees that every weld is executed with the same precision, ensuring the reliability and safety of beverage production lines.
High Production Rates: Due to its automated nature, orbital welding technology can maintain high production rates. This is especially useful in the beverage industry, which often requires extensive piping systems for large-scale production facilities.
The Process of Orbital Welding in the Beverage Industry
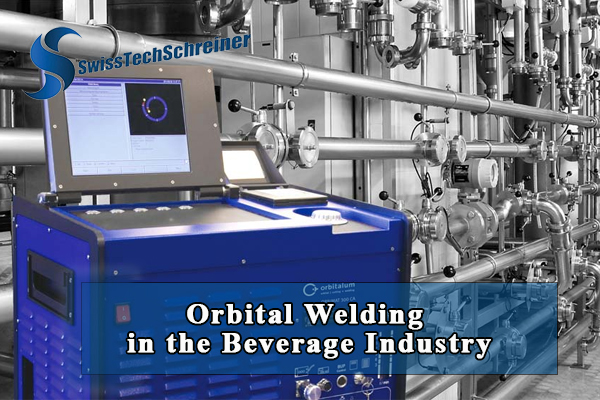
The orbital welding process begins by enclosing the pieces to be welded within a welding head. An electric arc is then formed from a tungsten electrode, which moves in a circular motion around the pipe, creating a perfect circumferential weld. The use of shielding gas, like argon, ensures that contaminants are kept at bay during the welding process.
=> Read more at : Beverage Industry Use Orbital Welding Technology Application
The Benefits Beyond Just Welding
While the primary benefit of orbital welding technology is the high-quality welds it produces, the technology brings along other advantages:
Cost-Efficiency: With reduced weld failures and the elimination of rework, the overall cost savings over time can be significant.
Reduced Training Costs: While the initial setup and programming of orbital welding machines may require specialized knowledge, the need for multiple skilled manual welders is decreased, leading to reduced training expenses.
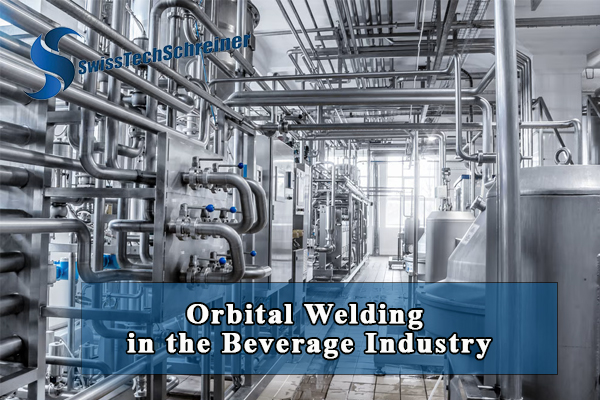
Flexibility: Modern orbital welding equipment can be programmed to handle various sizes and specifications, making it a versatile tool for different production requirements.
Orbital welding technology is revolutionizing the beverage industry by providing a solution that ensures product purity, operational efficiency, and unmatched consistency. As consumer demand for safety and quality in beverages continues to rise, we can only expect the adoption of such sophisticated technologies to become more widespread. If your business in the beverage industry is in need of pipeline system construction and installation using orbital welding technology, please contact Swisstech Schreiner for advice and support.
=> Read more about the Pipeline Construction in beverage industry at :
=> Orbital welding technology in the Pipeline Construction in beverage industry
Meets on-site standards in the beverage industry with orbital welding technology
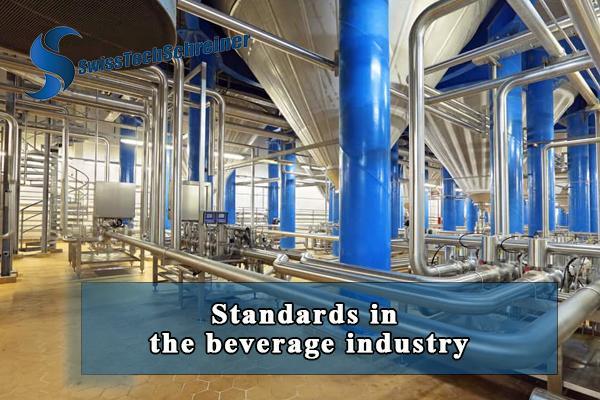
The stringent requirements of the beverage industry mean that specific standards guide orbital welding processes:
Surface Finish: The interior surface of welded tubes and pipes should be smooth, free from ridges, and have a finish that matches or exceeds the parent material. This ensures that there's minimal buildup or deposition inside the tubes, which can affect beverage flow or quality.
Inspection and Validation: The beverage industry often uses borescopes or other visual inspection tools to confirm the integrity of orbital welds. Some even employ advanced techniques like X-ray or ultrasonic testing for a more detailed assessment.
Documentation: Every weld, its parameters, and results are meticulously documented. This provides a clear traceability record, ensuring accountability and aiding in quality assurance.
Training and Qualification: Only certified welders, trained in the specifics of orbital welding for the beverage industry, are allowed to oversee or maintain the equipment. This ensures that the highest quality standards are upheld.
Orbital welding technology standards have firmly cemented their place in the beverage industry. The emphasis on purity, precision, and consistency ensures that the drinks we consume are not just delightful but also safe. To make sure that there's an amalgamation of advanced technology and rigorous standards at play, bringing customers that unparalleled taste and quality, contact Swisstech Schreiner for advice and support.
Swisstech Schreiner.
Add: ch 4153 reinach and hcm city vietnam
Hotline: (+84) 931 - 386 - 062
Phone: (+84) 931 - 386 - 062 +84931386062 ( zalo / viber / whatsapp )
Email: swiss.tech.schreiner@gmail.com
Other News

Maintenance work for the factory, why they need it
Specifically, Swisstech also provides maintenance work and equipment maintenance at the request of customers. We also provide MONTHLY, QUARTERLY, and YEARLY maintenance that is quick, professional, and honest.
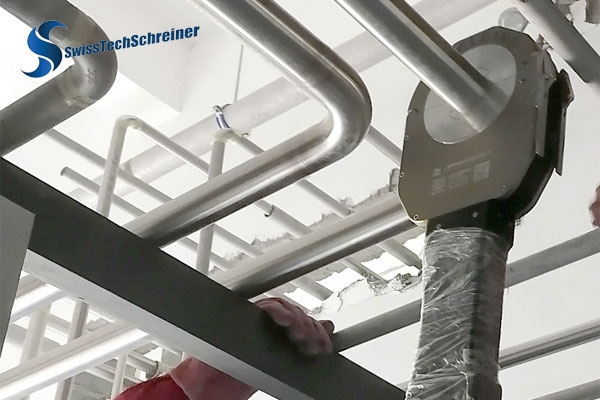
Precision and Durability Stainless Steel Pipe Processing
People often laud stainless steel for its strength, corrosion resistance, and aesthetic appeal. A significant facet of this material's utility lies in its transformation into pipes. Let's have Swisstech Schreiner delve into the world of stainless steel pipe processing.
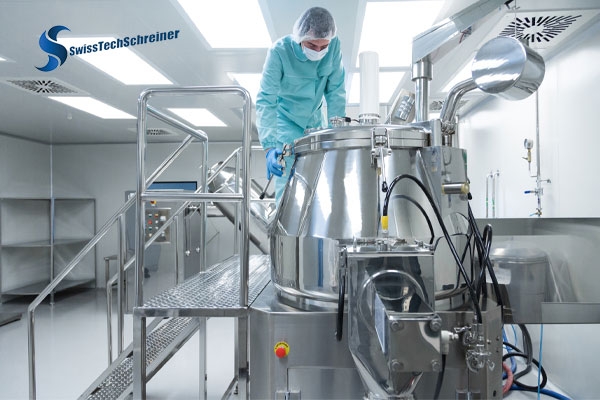
Lý Do Tại Sao Hàn Orbital Được Tin Dùng Trong Ngành Sữa
Ngày nay, hàn công nghệ quỹ đạo orbital welding technology đang trở thành xu hướng nổi bật trong nhiều ngành công nghiệp, đặc biệt là trong ngành sản xuất sữa. Hãy cùng tìm hiểu thêm chi tiết về công nghệ hàn thông qua bài sau.
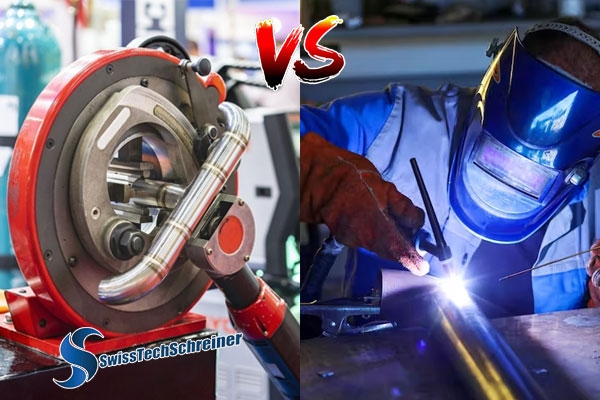
Comparing Orbital Welding Machine and Traditional Welding Methods
Explore with Swisstech Schreiner the efficiency of orbital welding machines versus traditional welding methods. Learn the advantages of orbital welding technology compare it to conventional welding techniques. Stay informed to make decisions for your welding projects.

Quá trình thực hiện Gia công Ống thép không gỉ ( Stainless steel pipe processing)
Khám phá quy trình sản xuất ống thép không gỉ ( Stainless steel pipe processing) từ nguyên liệu đến thành phẩm cuối cùng. Bài viết của Swisstech Schreiner giải thích chi tiết các bước sản xuất, bao gồm cả ống hàn và ống liền mạch, cũng như ứng dụng rộng rãi của chúng trong nhiều ngành công nghiệp.
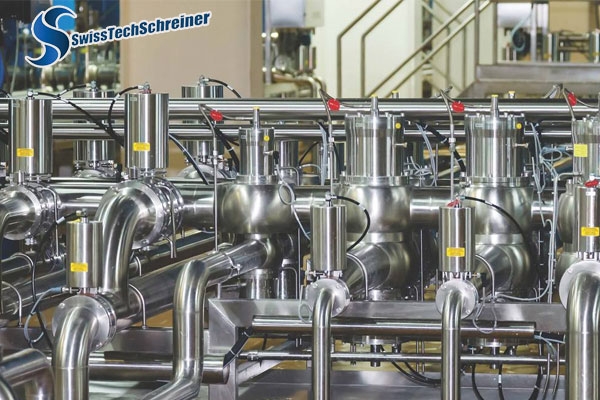
The Orbital Welding Technology in the Beverage Industry: Revolutionizing Quality and Efficiency
Discover how orbital welding technology is transforming the beverage industry, revolutionizing production quality and efficiency. Let's at Swisstech Schreiner explore the techniques and innovations that are raising the bar for beverage manufacturing in this exploration of orbital welding's impact.