Choosing the right pipe welding method is crucial for achieving high-quality, efficient, and cost-effective results in your welding projects. Among the various techniques available, orbital welding machine has emerged as a top choice for their precision, consistency, and ease of use. In this article, Swiss Schreiner will take the reader to orbital welding technology. Exploring its applications, and process to help you determine if it's the right method for your specific needs.
Applications and Industries of Orbital Welding machine
Orbital welding machines that are advanced technology and precision, have a broad range of applications across various industries. This section will provide a comprehensive look into the specific applications and industries where orbital welding is not just beneficial but often essential.
Applications of Orbital welding technology
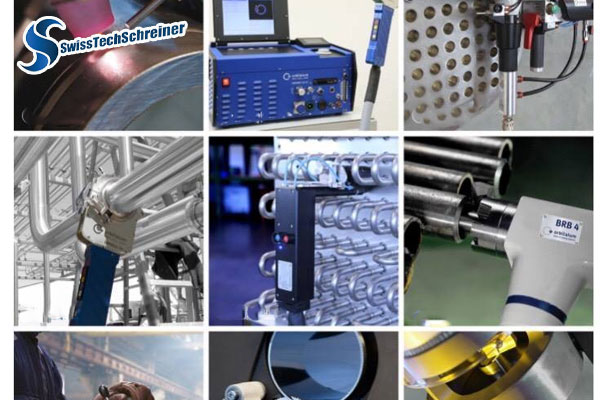
Piping Systems: Orbital welding technology is extensively used in the installation and maintenance of piping systems. This includes pipelines for water, gas, and other fluids, where leak-proof, high-integrity welds are crucial.
Pharmaceuticals and Biotech: In the pharmaceutical and biotech industries, orbital welding is employed to create ultra-clean, contaminant-free welds. This is particularly important for process lines that handle sensitive materials or products.
Semiconductor Manufacturing: The semiconductor industry requires extremely high levels of precision and cleanliness. Orbital welding is used to fabricate and install the intricate piping systems that are essential for the production of semiconductors.
Food and Beverage Industry: Here, orbital welding is applied to construct and repair piping systems that must meet stringent hygiene standards. The smooth, crevice-free welds produced by orbital welding machine are ideal for these applications.
Aerospace and Aviation: In aerospace and aviation, orbital welding is utilized for its ability to produce consistent, high-quality welds on critical components, often involving exotic or hard-to-weld materials.
Nuclear and Power Generation: For nuclear and power generation facilities, the reliability and safety of welds are paramount. Orbital welding offers the precision and repeatability needed for these high-stakes applications.
Industries applied Orbital welding machine

Petrochemical: The petrochemical industry relies heavily on orbital welding for constructing and maintaining its vast network of pipelines and process equipment. The high-quality welds produced are essential for ensuring safety and efficiency.
Automotive: In the automotive industry, orbital welding is used in the manufacturing of exhaust systems, fuel lines, and other components requiring durable and reliable welds.
Shipbuilding and Marine: The shipbuilding and marine industries benefit from orbital welding’s ability to perform in challenging environments, delivering robust welds that can withstand harsh maritime conditions.
Water Treatment and Environmental: Orbital welding plays a key role in water treatment and environmental projects, where pipelines and tanks need to be leak-proof to prevent contamination.
Construction and Infrastructure: In the construction and infrastructure sectors, orbital welding is utilized for large-scale projects involving pipelines, structural components, and other critical weldments.
Research and Development: In R&D, especially in laboratories and experimental setups, orbital welding is used for its precision and ability to handle a variety of materials and complex geometries.
Orbital welding machine has become indispensable in these industries and applications, providing unmatched quality, efficiency, and safety. Orbital welding technology produces consistent, high-quality welds in a variety of settings and materials. This makes them a valuable tool for any project that demands precision welding.
Pipe welding with Orbital Welding technology Process
Orbital welding technology has streamlined and optimized the pipe welding process, ensuring precision and consistency in every phase. This advanced method comprises several critical steps, each playing a pivotal role in achieving a flawless weld.
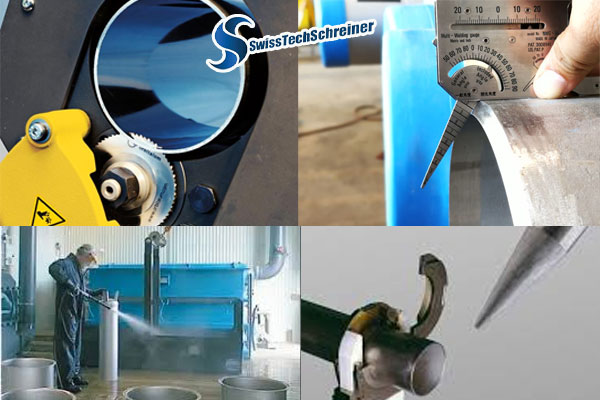
Step 1. Cut
The process begins with cutting the pipe. It's vital that the cut is clean and square to ensure that the edges align perfectly during welding. This precision in cutting sets the foundation for a high-quality weld.
Step 2. Face or Bevel
Next, we move to facing or beveling the pipe ends. This step is about preparing the edges of the pipe for welding, creating a bevel that matches the welding specifications. The accuracy in this step is crucial as it affects the weld's integrity and strength.
Step 3. Clean
The third step is cleaning the pipe. This involves removing any contaminants like oils, dirt, or oxides from the pipe's surface. Cleanliness is paramount in orbital welding, as even the smallest impurity can compromise the weld quality.
Step 4. Tungsten
Then comes the preparation of the tungsten electrode, which is central to the welding process. The tungsten must be ground to a point, ensuring optimal arc control and penetration. The quality of the tungsten preparation significantly influences the welding arc's stability and consistency.
=> See more articles on the same topic at :
=> (Orbital welding machine) Máy hàn quỹ đạo: giải pháp hiệu suất dành cho doanh nghiệp
=> TIG Orbital Welding Machine - Thiết bị hàn quỹ đạo TIG
=> Reasons why orbital welding machines are suitable for pipe welding
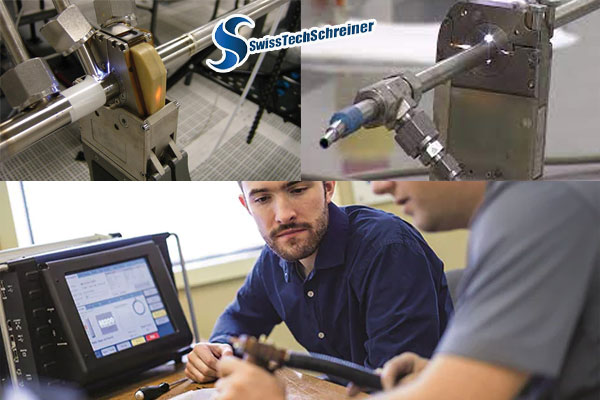
Step 5. Align
Aligning the pipes is the next critical phase. Perfect alignment ensures uniform welds and helps avoid defects like misalignment or gaps between the pipe sections. This step often uses specialized clamps to maintain alignment during welding.
Step 6. Purge
Purging is another essential step. This involves filling the pipe with an inert gas, usually argon, to displace any air and prevent oxidation during welding. Purging is crucial for maintaining the purity and quality of the weld, especially when working with materials like stainless steel.
Step 7. Program
Finally, the process culminates with programming the orbital welding machine. This involves setting the welding parameters such as current, speed, and gas flow. The programming must be precise to ensure that the welding process is optimized for the specific pipe material and thickness.
Each of these steps is integral to the orbital welding process, ensuring that the final weld is of the highest quality. The precision and control offered by orbital welding technology make it a superior choice for a wide range of applications, promising consistency, efficiency, and exceptional weld integrity.
Orbital welding machine stands out for its automated process, which minimizes human error and ensures uniform welds, especially in challenging pipe configurations and environments. This technology has revolutionized industries such as aerospace, pharmaceuticals, and petrochemicals, where high standards of weld integrity and repeatability are paramount.
Swisstech Schreiner.
Add: ch 4153 reinach and hcm city vietnam
Hotline: (+84) 931 - 386 - 062
Phone: (+84) 931 - 386 - 062 +84931386062 ( zalo / viber / whatsapp )
Email: swiss.tech.schreiner@gmail.com
Other News
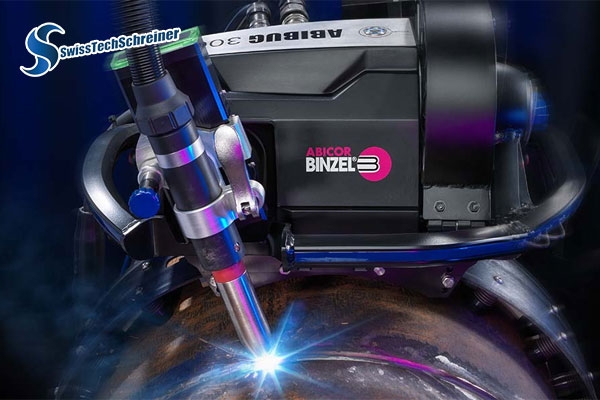
Công nghệ hàn quỹ đạo cho đường ống kích thước lớn
Cùng Swisstech Schreiner khám phá công nghệ hàn quỹ đạo Orbital welding technology tiên tiến dành cho đường ống kích thước lớn, một giải pháp hiệu quả và đáng tin cậy để đảm bảo mối hàn chất lượng cao và độ bền vượt trội.
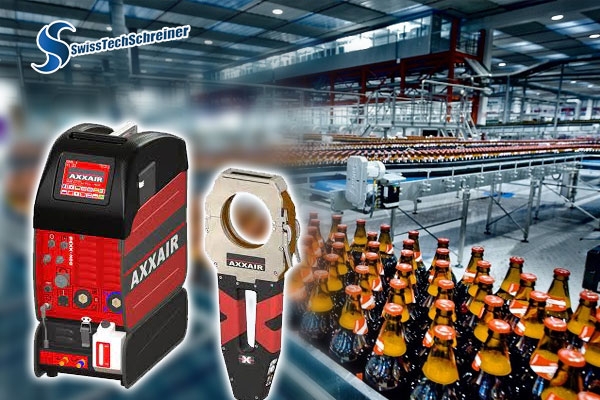
SwissTech Cung cấp hàn quỹ đạo ngành nước giải khát (Beverage Industry)
Nếu doanh nghiệp của bạn đang tìm kiếm một đơn vị cung cấp thiết bị máy hàn orbital cũng như các giải pháp thi công, lắp đặt đường ống chất lượng cao, hãy liên hệ với SwissTech. Chúng tôi cam kết mang lại giải pháp tối ưu nhất, đáp ứng mọi yêu cầu khắt khe của khách hàng trong các ngành công nghiệp quan trọng.
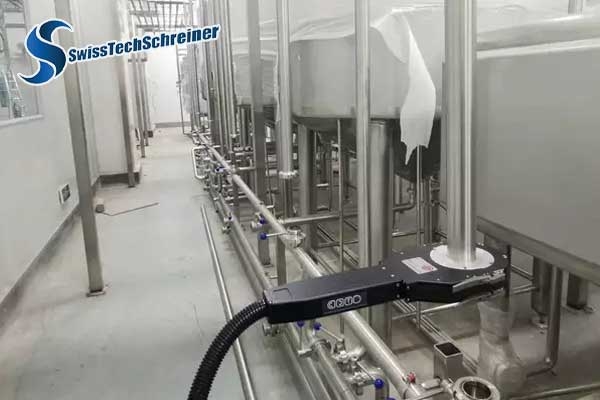
Máy hàn quỹ đạo trong thi công hệ thống đường ống
Giới thiệu chi tiết quy trình hàn đường ống bằng máy hàn quỹ đạo, các bước chuẩn bị, vận hành và bảo dưỡng máy. Hãy cùng Swisstech Schreiner tìm hiểu về ứng dụng máy hàn quỹ đạo Orbital welding machine trong các ngành công nghiệp qua bài viết sau.

Various orbital welding machine applications
In an orbital welding machine, a process runs under computer control with very little intervention from the operator. This process is specifically used for repeatable welding and high-quality welding.
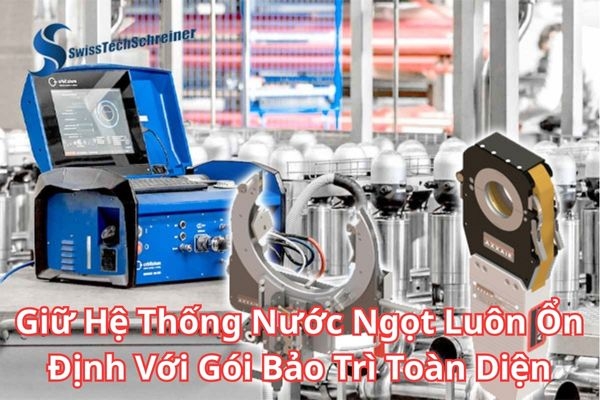
Giữ Hệ Thống Nước Ngọt Luôn Ổn Định Với Gói Bảo Trì Toàn Diện
Với đội ngũ kỹ thuật viên nhiều kinh nghiệm và hệ thống thiết bị hiện đại, Swisstech Schreiner cung cấp dịch vụ bảo trì hệ thống nước ngọt uy tín, chuyên nghiệp cho nhà máy, khu công nghiệp và các tổ hợp sản xuất.
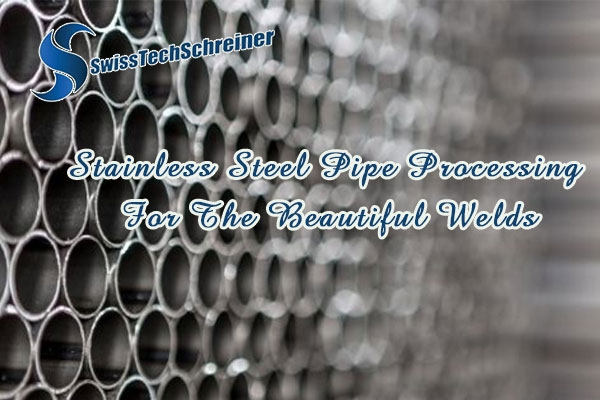
Stainless Steel Pipe Processing For The Beautiful Welds
For those on the lookout for the zenith of precision in stainless steel pipe processing , Swisstech Schreiner promises an unparalleled experience. Dive deeper into the nuances of orbital welding technology and steel pipe processing with us. For more insights and collaborations, don't hesitate to reach out. Your journey to welding excellence is just a call away with Swisstech Schreiner .