Orbital welding machines have revolutionized the pipe welding industry with their precision, efficiency, and unmatched consistency. In the following sections, we delve into the specifics of why orbital welding machines are the premier choice for professional pipe welding tasks. Join Swisstech Schreiner as we uncover the reasons behind the orbital welding technology growing prevalence and how they could be the key to unlocking new levels of excellence in pipe welding.
Precision and Consistency
Precision and Consistency are paramount in the world of pipe welding. Orbital welding machines offer a level of accuracy that is virtually unattainable with manual welding. These engineering utilize sophisticated computer programming to control the welding torch, allowing for precise weld penetration and consistent bead placement. This precision ensures that every weld is consistent with the last, significantly reducing the potential for defects and non-compliance with welding codes.
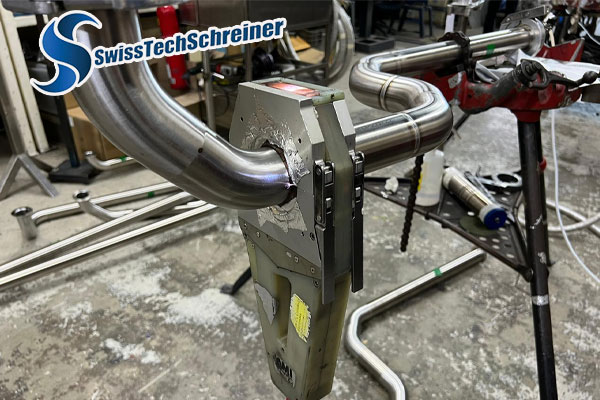
Enhanced Productivity
The enhanced productivity provided by orbital welding machine is a game-changer for the industry. When compared to manual welding, orbital welding technology is not just faster, but also more efficient. This is because the machine can work continuously without the need for breaks, and the welding parameters can be pre-set, reducing the setup time between welds. Case studies from various industries showcase a marked increase in output rates when switching to orbital welding. For instance, a pharmaceutical company reported a 60% reduction in welding time after implementing orbital systems, highlighting the profound impact on productivity.
Superior Weld Quality
When it comes to Superior Weld Quality, orbital welding machines are in a league of their own. They operate in a controlled environment, which is critical in maintaining weld integrity. The closed chamber in which the weld is performed is shielded from external contaminants, significantly reducing the chances of weld contamination. This is particularly crucial in industries where purity and cleanliness are non-negotiable, such as in semiconductor or food processing plants or beverage industry.
Operator Safety
Operator Safety is significantly enhanced with orbital welding machines. Orbital welding technology is designed to take on the high-risk elements of welding, thereby reducing the risks associated with manual welding. With features that promote an ergonomic work environment, these machines help in minimizing operator fatigue and exposure to harmful welding fumes and intense light.
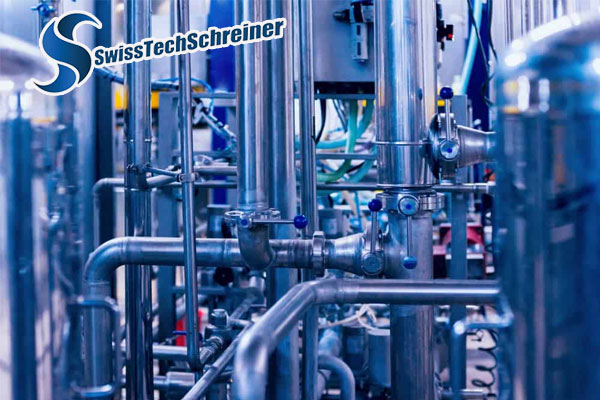
Versatility Across Materials and Environments
Versatility Across Materials and Environments is another feather in the cap for orbital welding machines. They are adept at handling a wide range of materials including stainless steel, titanium, and other exotic alloys. Additionally, orbital welding technology can operate effectively in various environmental conditions and in positions that would be challenging for a human welder, such as in confined spaces or overhead welding.
Cost-Effectiveness Over Time
The Cost-Effectiveness Over Time of using orbital welding machine systems becomes apparent when considering the long-term operational costs. These systems minimize material wastage and the need for rework due to their high-quality welds, translating into significant cost savings. Furthermore, the improved weld strength and durability mean less maintenance and longer lifespans for the welded structures.
Compliance with Industry Standards
Compliance with Industry Standards is critical, and orbital welding machines excel at ensuring adherence to these standards. They are designed to meet the stringent quality requirements set by industry regulators, making the certification and compliance process smoother and more reliable.
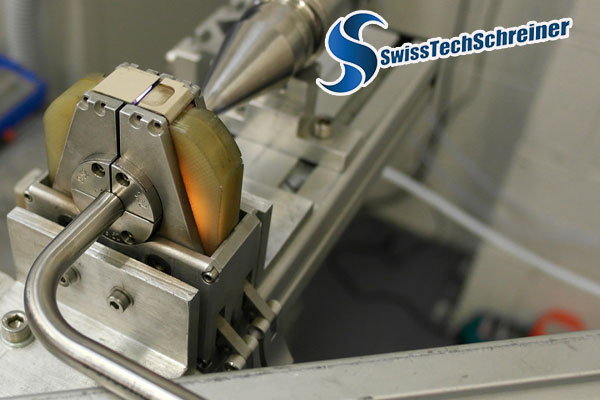
Advanced Data Recording and Traceability
Lastly, Advanced Data Recording and Traceability is an integral aspect of orbital welding technology. The ability to record detailed data about each weld helps in quality assurance and provides a traceable record for future reference. This data includes parameters such as weld heat input, time, and gas flow rates, which are essential for quality control and certification purposes.
=> See more articles on the same topic at :
=> (Orbital welding machine) Máy hàn quỹ đạo: giải pháp hiệu suất dành cho doanh nghiệp
=> TIG Orbital Welding Machine - Thiết bị hàn quỹ đạo TIG
=> Cách hoạt động máy hàn quỹ đạo (orbital welding machine) để hàn ống và đường ống
Orbital welding machines offer a multitude of benefits that are hard to overlook. From ensuring precision and consistency in each weld to enhancing productivity and ensuring operator safety, these machines are transforming pipe welding into a high-tech, efficient, and reliable process that meets the demands of modern industry. Their ability to weld a variety of materials in diverse conditions, coupled with their cost-effectiveness and compliance capabilities, positions orbital welding technology as a cornerstone technology in the fabrication industry.
The orbital welding technology caters to the increasing demands for quality and safety in sectors such as aerospace, pharmaceuticals, and semiconductor manufacturing, where perfect welds are not just desired but essential. The suitability of orbital welding systems for pipe welding is grounded in their ability to automate the welding process, minimizing human error and ensuring a higher standard of weld integrity.
From their advanced control systems that guarantee repeatable results to their adaptability to various materials and environments, these machines represent the pinnacle of welding technology. Contact Swisstech Schreiner if you need advice and support on any issues related to purchasing, selling, investing in orbital welding machine systems, applying orbital welding technology in pipeline construction, training, and maintenance. maintenance,... at the following contact information.
Swisstech Schreiner.
Add: ch 4153 reinach and hcm city vietnam
Hotline: (+84) 931 - 386 - 062
Phone: (+84) 931 - 386 - 062 +84931386062 ( zalo / viber / whatsapp )
Email: swiss.tech.schreiner@gmail.com
Other News
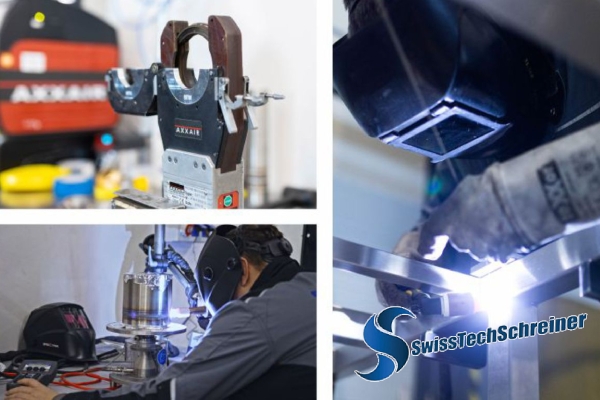
Các kỹ thuật hàn quỹ đạo trong ống dẫn dược phẩm
Các kỹ thuật hàn quỹ đạo - Orbital welding technology cung cấp giải pháp lý tưởng cho các thách thức về vệ sinh và kín khí trong môi trường sản xuất dược phẩm. Bài viết này của Swisstech Schreiner sẽ khám phá chi tiết về các kỹ thuật hàn quỹ đạo phổ biến.

Lợi ích của máy hàn quỹ đạo (orbital welding machine) so với máy hàn truyền thống
Máy hàn quỹ đạo (orbital welding machine) một giải pháp hiện đại, vượt trội so với các phương pháp hàn truyền thống nhờ vào khả năng cung cấp mối hàn chính xác, đồng đều, và chất lượng cao. Hãy cùng Swisstech Schreiner khám phá những lợi ích mà máy hàn orbital mang lại qua bài viết sau.
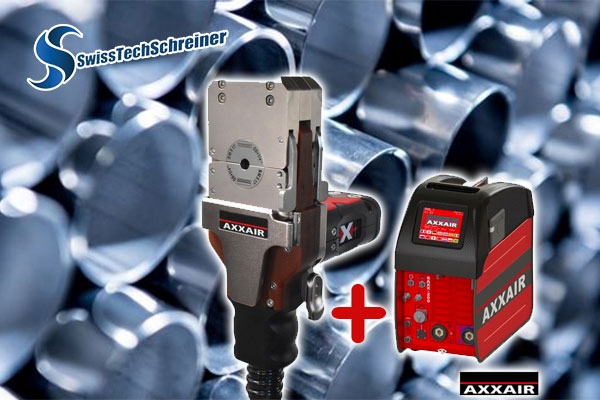
Mẹo hàn gia công ống thép không gỉ Stainless steel pipe processing
Khám phá các mẹo hàn gia công ống thép không gỉ Stainless steel pipe processing hiệu quả và nhanh chóng. Cùng Swisstech Schreiner tìm hiểu cách xử lý và cải thiện chất lượng mối hàn, giúp công trình của bạn bền vững hơn
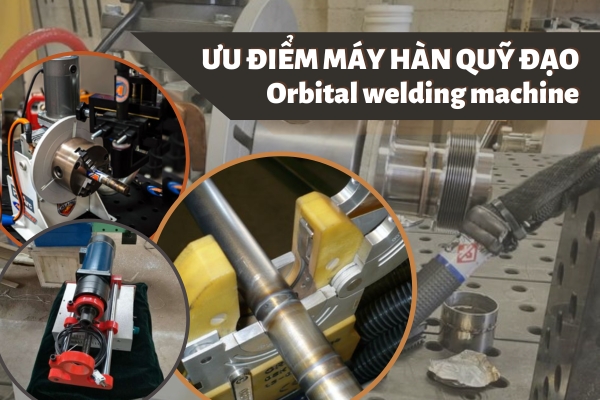
Ưu điểm của máy hàn quỹ đạo (orbital welding machine) trong ngành công nghiệp hiện đại
Hiện nay, nhu cầu sửa chữa và bảo trì các thiết bị, máy móc trong các khu công nghiệp và nhà máy rất lớn. Máy hàn quỹ đạo (orbital welding machine) đã trở thành công cụ quan trọng trong việc bảo trì và sửa chữa các bộ phận máy móc, nhất là trong ngành công nghiệp. Trong bài viết này, hãy cùng Swisstech Schreiner tìm hiểu về ưu điểm khi sử dụng máy hàn quỹ đạo trong ngành công nghiệp hiện đại.
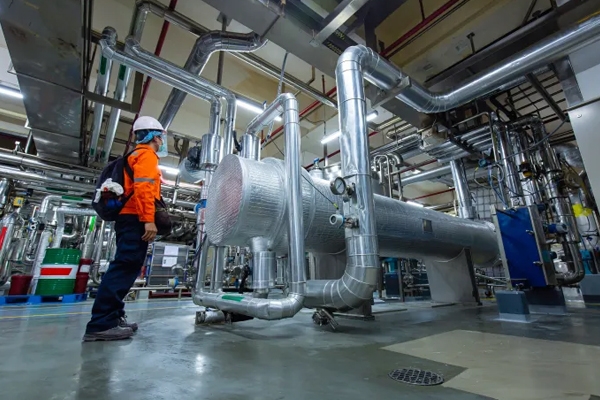
Gia công ống thép không gỉ (Stainless steel pipe processing) cho mối hàn đẹp
Ống thép không gỉ là loại vật liệu có khả năng chống ăn mòn cao, bền, đẹp và dễ gia công.. Tuy nhiên để đảm bảo an toàn của các sản phẩm ống thép, cần phải tuân thủ các kỹ thuật hàn chuyên nghiệp để tạo ra những mối hàn đẹp. Hãy theo dõi bài viết sau của Swisstech Schreiner để hiểu rõ hơn những phương pháp và lưu ý khi gia công ống thép không gỉ (Stainless steel pipe processing) nhé.
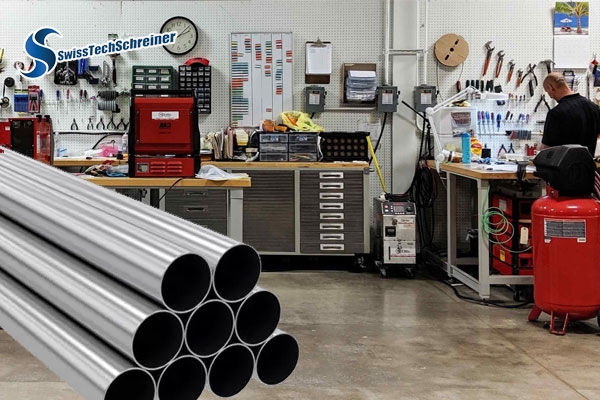
Những ngành cần ứng dụng gia công ống thép không gỉ - stainless steel pipe processing
Ngành công nghiệp sản xuất và nhà máy đặc biệt cần đến gia công ống thép không gỉ (stainless steel pipe processing) do khả năng chịu ăn mòn cao, dễ vệ sinh và tiệt trùng hơi. Hãy cùng Swisstech Schreiner tìm hiểu kỹ hơn các ngành ưa chuộng ứng dụng này qua bài viết sau.nước của chúng.