The advent of orbital welding technology has changed the landscape of welding industries, from aerospace to orbital pharmaceutical and beyond. Offering an extensive range of benefits, it's not just about welding in a circle. Here's why choosing this technology could be one of your most forward-thinking decisions. Let's explore orbital welding technology more deeply with Swisstech Schreiner through the following article
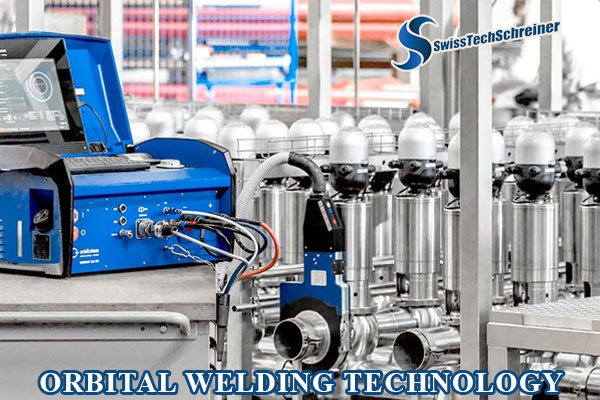
Open Platform Design
Orbital welding machines often come with an open platform design. This doesn't only ensure that the system is easy to set up and maintain, but it also means it can be upgraded as technology advances. An open design ensures adaptability, future-proofing your investment and allowing integration with new software and hardware innovations.
Automation
One of the most compelling reasons to opt for orbital welding technology is the degree of automation it offers. Human error is a consistent challenge in welding. With the automated functions of orbital welding systems, you get enhanced accuracy, precision, and consistency in every weld. This reduces defects and increases the overall quality and reliability of your projects.
Programming
Programming capabilities make orbital welding machines highly adaptable to varied job requirements. Users can store numerous weld programs and easily recall them, ensuring efficiency for both repeated jobs and new projects. This feature ensures that the machine can cater to diverse welding needs, making it a versatile asset for any workshop.
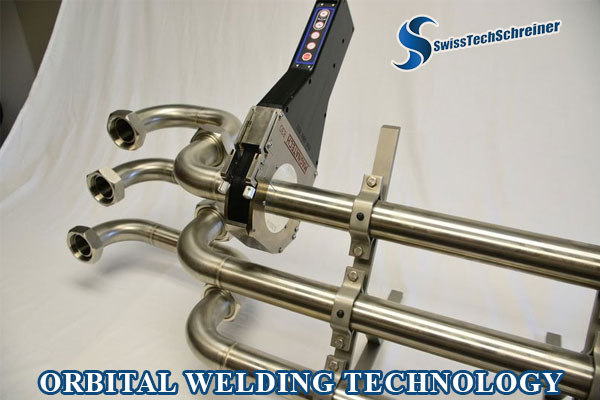
Documentation
In industries where traceability and compliance are crucial, the documentation feature of orbital welding becomes indispensable. Modern orbital welding machines can provide detailed records of every weld, capturing parameters like heat input, time, and gas flow. This digital documentation is crucial for quality assurance and meeting regulatory standards.
Weld Repeatability
Orbital welding technology offers unmatched repeatability. Once you've set the parameters for a particular weld, the machine can reproduce the same high-quality weld again and again, ensuring consistent results throughout the project. This reduces the variance often associated with manual welding and guarantees a standardized output.
=> Read more : Orbital Welding Technology Standards in the Beverage Industry
Gas Control
Effective gas control is critical for many welding processes to prevent oxidation and contamination. Orbital welding systems offer precise gas control, ensuring that welds are consistently protected, leading to cleaner, more reliable joints.
Blast Purge
The blast purge feature in orbital welding machines clears the weld zone of any contaminants before the welding process begins. This ensures a cleaner weld zone, which is vital for industries where even the minutest contamination can compromise the integrity of a weld.
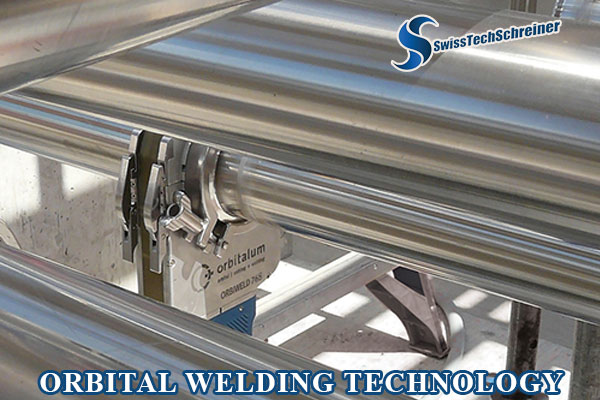
Power Considerations
Orbital welding machines are designed to be energy-efficient. They regulate power consumption based on the specific needs of the weld, ensuring optimal use of energy. This not only leads to cost savings but also makes the technology more environmentally friendly.
Portability and Accessibility
Despite the advanced technology they pack, many orbital welding systems are compact and portable. This makes them ideal for on-site jobs and projects in confined spaces. Their design ensures accessibility, allowing welders to handle complex geometries and hard-to-reach areas with ease.
Orbital welding technology provides a blend of precision, consistency, and versatility, making it a pivotal choice for industries seeking high-quality welding solutions. Its range of features ensures adaptability and efficiency, reinforcing its position as a future-oriented welding solution.
=> Read more : The Orbital Welding Technology in the Beverage Industry: Revolutionizing Quality and Efficiency
Orbital welding machine at Swisstech Schreiner for pipeline construction
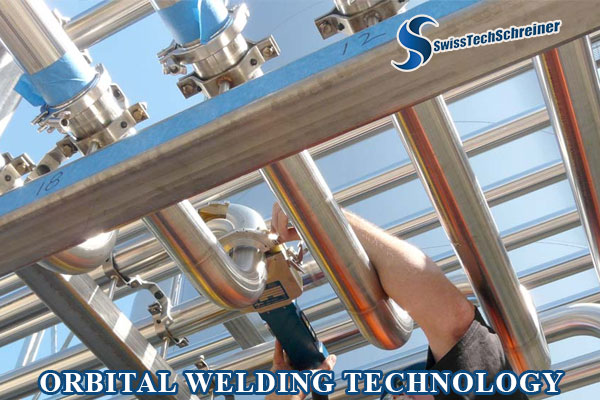
Orbital welding technology a changer in the welding industry, has been given a fresh dimension by Swisstech Schreiner, especially for pipeline construction in industries such as beverage industry, pharmaceutical industry,.... With this innovative solution, pipeline projects can now boast higher precision, improved reliability, and faster turnaround times.
Swisstech Schreiner's orbital welding machine brings unparalleled precision to the table. With its advanced sensors and calibration capabilities, every weld is executed with meticulous accuracy. This precision ensures that pipelines constructed using this device stand the test of time and offer robust performance.
Automation is the backbone of Swisstech Schreiner's offering. By minimizing human error, the device guarantees consistently high-quality welds. This is particularly crucial for pipelines that are subjected to extreme conditions and need to be free from vulnerabilities.
One of the standout features of the Swisstech Schreiner orbital welding machine is its intuitive user interface. Whether you're a novice or a seasoned welding professional, the device's controls and settings are easy to navigate, making the welding process seamless and efficient.
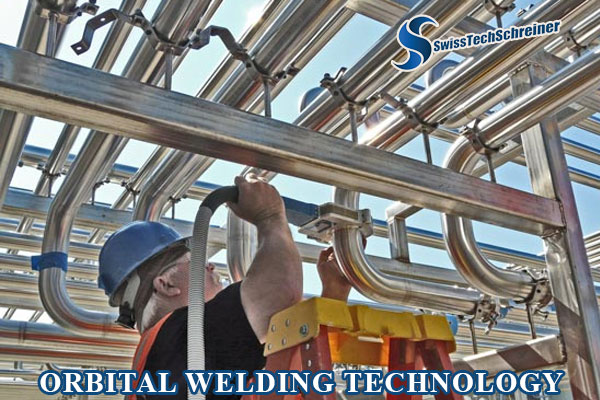
Pipeline construction in industries comes with its set of hazards. Recognizing this, Swisstech Schreiner has incorporated cutting-edge safety features into their orbital welding technology. From automated shut-offs to protective barriers, every safety concern has been addressed, ensuring the well-being of operators.
No two pipeline projects are the same. Swisstech Schreiner's device offers the flexibility to cater to diverse project requirements. Whether it's challenging terrain or a complex pipeline configuration, the device is designed to adapt and deliver outstanding results.
=> Read more at : Swisstech Schreiner and Construct Pipelines in the Beverage Industry
Time is often of the essence in pipeline construction. With the speed and efficiency of the Swisstech Schreiner orbital welding device, project completion times are significantly reduced. This means faster deployments and quicker returns on investment for stakeholders.
Choosing Swisstech Schreiner isn't just about investing in a top-of-the-line welding device; it's also about tapping into a network of dedicated support. With their comprehensive after-sales service, any queries, concerns, or technical hitches are swiftly addressed, ensuring smooth operations.
In the realm of pipeline construction for the pharmaceutical, bio, beverage industry , Swisstech Schreiner's orbital welding machine stands out as a beacon of innovation and reliability. For contractors and industry players aiming for perfection in every weld, this device is the key to achieving such lofty standards. Dive into the future of pipeline construction with Swisstech Schreiner. Contact us at :
Swisstech Schreiner.
Add: ch 4153 reinach and hcm city vietnam
Hotline: (+84) 931 - 386 - 062
Phone: (+84) 931 - 386 - 062 +84931386062 ( zalo / viber / whatsapp )
Email: swiss.tech.schreiner@gmail.com
Other News
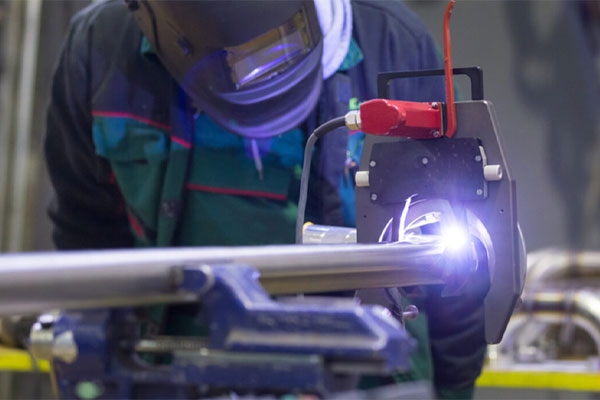
Máy hàn quỹ đạo - giải pháp tốt nhất cho mối hàn chất lượng cao
Công nghệ ứng dụng máy hàn quỹ đạo đang dần khẳng định vị thế trong các ngành công nghiệp đòi hỏi sự chuẩn xác cao, giúp tối ưu hóa hiệu quả và nâng cao chất lượng sản phẩm cuối cùng. Hãy cùng Swisstech Schreiner tìm hiểu thông qua bài viết dưới đây.
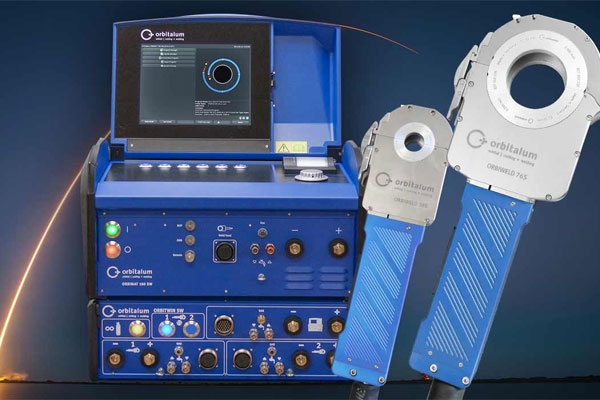
Đào tạo thợ hàn mới: Bí quyết giúp tăng tốc quy trình sản xuất
Khám phá các mẹo giúp doanh nghiệp rút ngắn thời gian đào tạo thợ hàn mới: từ công nghệ hàn quỹ đạo Orbital welding technology hiện đại, giám sát dữ liệu mối hàn đến tối ưu vật liệu và quy trình hàn. Nâng cao năng suất, tiết kiệm chi phí ngay hôm nay.
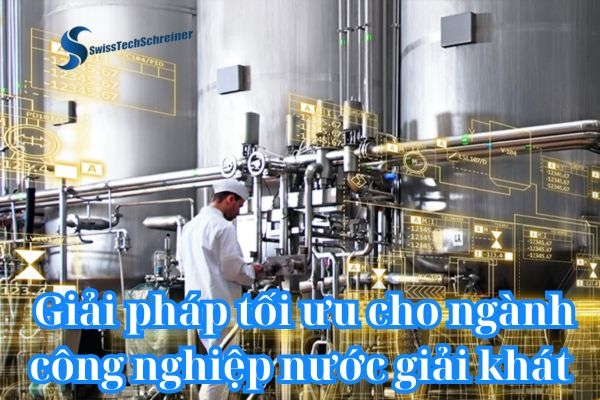
Beverage industry - Giải pháp tối ưu cho ngành công nghiệp nước giải khát
Công nghệ hàn quỹ đạo là bước tiến quan trọng giúp ngành công nghiệp nước giải khát nâng cao chất lượng sản phẩm và tối ưu hóa quy trình sản xuất. Việc đầu tư vào công nghệ này không chỉ giúp các doanh nghiệp đáp ứng các tiêu chuẩn quốc tế mà còn tạo lợi thế cạnh tranh bền vững trên thị trường.
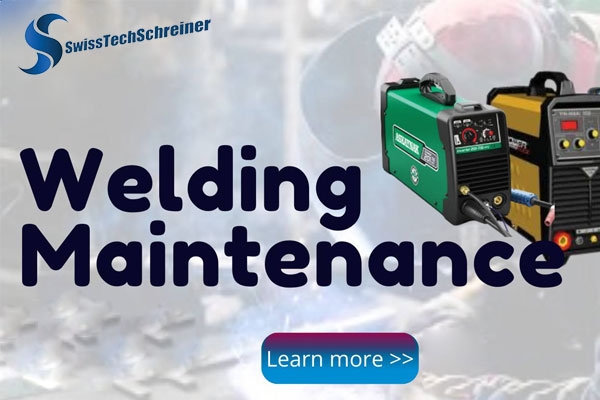
Bảo dưỡng thiết bị hàn (Maintenance work of welding equipment)
Cho dù đó là thiết bị hàn khí, hồ quang hay điện trở, việc thực hiện các công tác bảo trì máy hàn (maintenance work of welding machine) có thể giúp chúng ta tiết kiệm được những chi phí lớn trong tương lai. Hãy cùng Swisstech Schreiner tìm hiểu quy trình và phương pháp bảo dưỡng (maintenance work) các loại máy hàn qua bài viết sau.
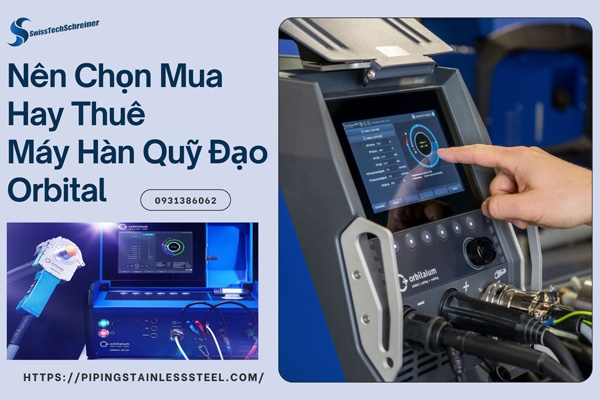
Nên Chọn Mua Hay Thuê Máy Hàn Quỹ Đạo Orbital
Máy hàn quỹ đạo Orbital (Orbital welding machine) - Công cụ không thể thiếu trong các ngành công nghiệp, tạo nên mối hàn nhất quán, chất lượng cao. Công nghệ hàn quỹ đạo phục vụ cho tất cả các ngành từ hàng không vũ trụ, ô tô, dược phẩm và thực phẩm,...
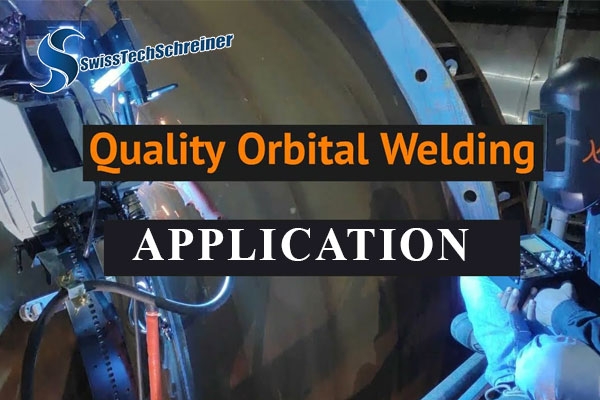
Application of Orbital Welding Technology in the Construction of Industrial Pipeline Systems
Enter orbital welding technology in the construction and maintenance of industrial pipeline systems. Let's Swisstech Schreiner delve into the fascinating realm of orbital welding and its transformative impact on pipeline construction.