In the dynamic world of the beverage industry, where quality, efficiency, and hygiene hold paramount importance, innovations in manufacturing and assembly processes play a critical role in upholding standards and driving success. One technological advancement that has significantly transformed the landscape of beverage production is orbital welding technology.
This method of welding has gained immense popularity and become a preferred choice for many beverage manufacturers, thanks to its unparalleled precision, consistency, and reliability. In this comprehensive guide, Swisstech Schreiner delves into the core reasons why the beverage industry is increasingly opting for orbital welding technology, highlighting its remarkable benefits and showcasing real-world applications that underscore its indispensability.
What is orbital welding technology in the beverage industry?
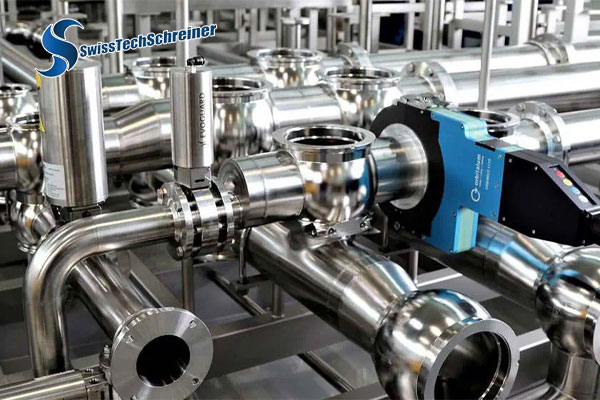
Orbital welding technology in the beverage industry represents a groundbreaking shift, offering unparalleled precision, consistency, and hygiene in the assembly and maintenance of piping systems. This advanced welding technique utilizes computer-controlled processes, ensuring that every weld is performed with exacting accuracy, a crucial factor in an industry where even the slightest contamination can lead to product spoilage and significant financial losses.
By automating the welding process, orbital welding minimizes human error, resulting in stronger, more reliable welds that stand up to the rigorous demands of beverage production. The technology is particularly beneficial for working with stainless steel tubing, a material commonly used in the industry due to its corrosion-resistant properties.
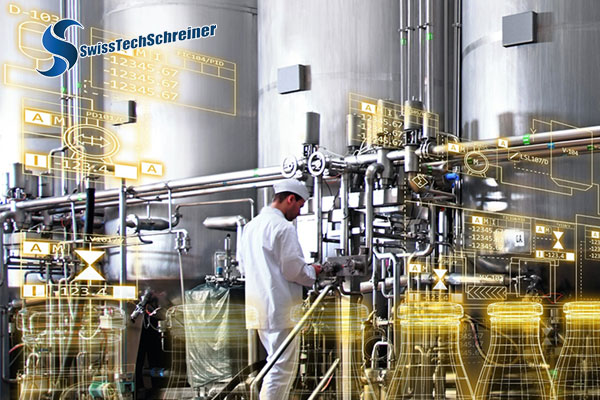
The seamless and crevice-free welds achieved with orbital welding technology are critical in preventing the accumulation of bacteria and ensuring the integrity of the product throughout the production cycle. Moreover, the speed and efficiency of orbital welding not only expedite project timelines but also contribute to cost savings, making it an economically sound choice for beverage manufacturers.
Additionally, the ability to replicate precise welds across numerous applications ensures uniformity and standardization, further enhancing the quality control measures within the industry. Orbital welding’s contribution to maintaining the pristine condition of the internal surfaces of tubing and pipes cannot be overstated, as it plays a direct role in ensuring that the final product meets the highest standards of quality and safety.
The reason why the beverage industry chooses orbital welding technology

The beverage industry’s inclination toward orbital welding technology stems from its relentless pursuit of excellence, precision, and hygiene, as these factors directly correlate with the quality and safety of the final product. Orbital welding technology, with its computer-controlled precision, guarantees impeccable welds, ensuring that the piping systems used in beverage production are secure, leak-proof, and free from contaminants.
The seamless welds created by this advanced method eliminate crevices that could harbor bacteria, thus maintaining the purity of the beverages and ensuring compliance with stringent health and safety standards. Furthermore, the consistency provided by orbital welding ensures uniformity across all welding operations, a critical aspect for large-scale manufacturers aiming to maintain product consistency across different batches and locations.
The industry’s adoption of this technology also aligns with its commitment to efficiency and cost-effectiveness. Orbital welding not only speeds up the assembly process but also reduces the need for post-weld cleanups and revisions, directly translating to time and cost savings.
The durability of the welds ensures longevity and reduces the need for frequent maintenance, providing long-term financial benefits. Moreover, the versatility of orbital welding makes it suitable for various applications within the beverage production process, from connecting process piping to assembling intricate components, making it a one-stop solution for diverse welding needs.
=> Read more at :
=> Considerations for Orbital Welding Technology in BioProcess Piping Application
=> Orbital Welding Technology for Pipeline Systems Construction
=> How to Use Orbital Welding Technology Properly: A Comprehensive Guide
Swisstech Schreiner provide the orbital welding technology solution for the business in the beverage industry
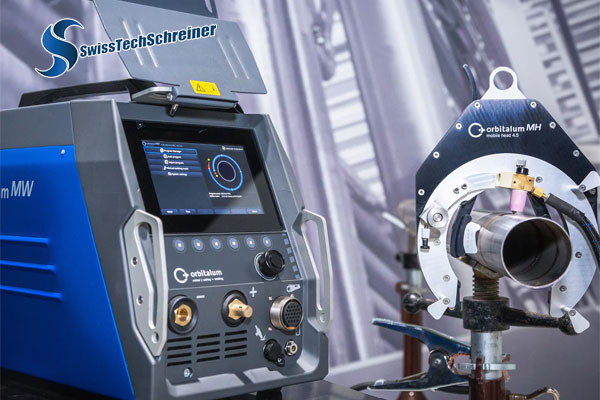
Swisstech Schreiner stands out as a pivotal player in revolutionizing the beverage industry, offering cutting-edge orbital welding technology solutions tailored to meet the unique demands of businesses within this sector. Their expertise in providing high-precision, reliable welding equipment ensures that manufacturers have access to the best tools necessary for maintaining the integrity, purity, and safety of their products. Swisstech Schreiner’s commitment to innovation is evident in their continual efforts to refine and enhance their orbital welding solutions, keeping pace with the evolving needs of the beverage industry.
The company’s holistic approach extends beyond just supplying equipment; they offer comprehensive support and training, ensuring that their clients can fully leverage the advantages of orbital welding technology. This commitment to customer success has positioned Swisstech Schreiner as a trusted partner for beverage manufacturers looking to optimize their production processes, reduce downtime, and maintain the highest standards of quality and safety. Their solutions are not just about facilitating seamless welds; they are about fostering operational excellence and driving industry advancements.
Swisstech Schreiner.
Add: ch 4153 reinach and hcm city vietnam
Hotline: (+84) 931 - 386 - 062
Phone: (+84) 931 - 386 - 062 +84931386062 ( zalo / viber / whatsapp )
Email: swiss.tech.schreiner@gmail.com
Other News
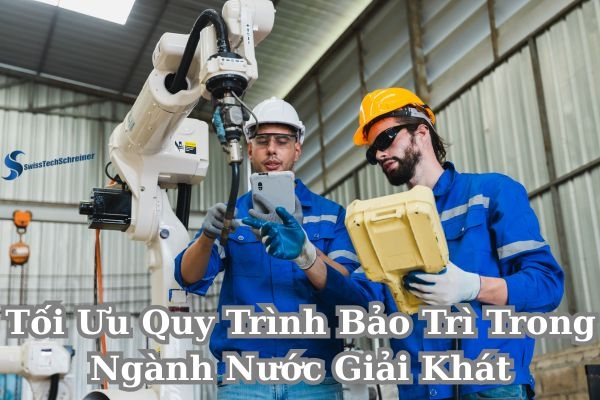
Tối Ưu Quy Trình Bảo Trì Trong Ngành Nước Giải Khát: Bảo Đảm Chất Lượng & Hiệu Suất Vượt Trội
Trong ngành đồ uống, bảo trì thiết bị đóng vai trò then chốt để đảm bảo chất lượng sản phẩm và an toàn sức khỏe người tiêu dùng. Tuy nhiên, đây cũng là khâu đầy thách thức do yêu cầu khắt khe và máy móc hiện đại.
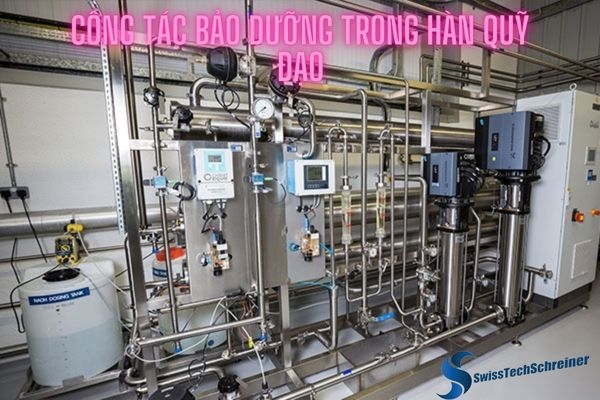
Công Tác Bảo Dưỡng Trong Hàn Quỹ Đạo (Maintenance work)
Tìm hiểu vai trò của công tác bảo dưỡng trong hệ thống hàn quỹ đạo. Giải pháp kiểm tra định kỳ, sửa chữa và ngăn ngừa sự cố giúp nhà máy vận hành an toàn, hiệu quả.
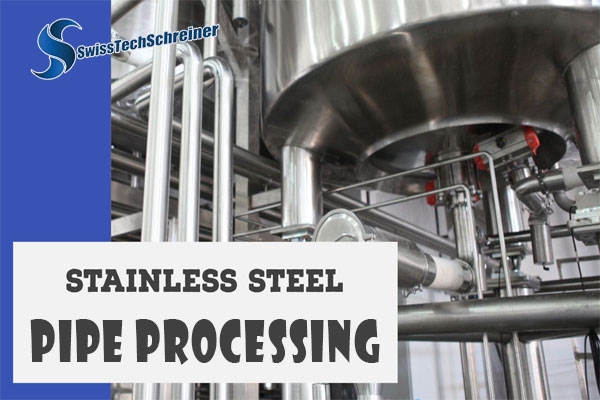
Tối Ưu Khả Năng Gia Công Ống Thép Không Gỉ với Quy Trình Hàn Orbital
Tìm hiểu cách tối ưu khả năng gia công ống thép không gỉ Stainless steel pipe processing với quy trình hàn orbital. Khám phá vì sao hàn inox khó khăn và cách giải pháp giúp tăng độ bền, chống ăn mòn, và đảm bảo chất lượng mối hàn vượt trội.
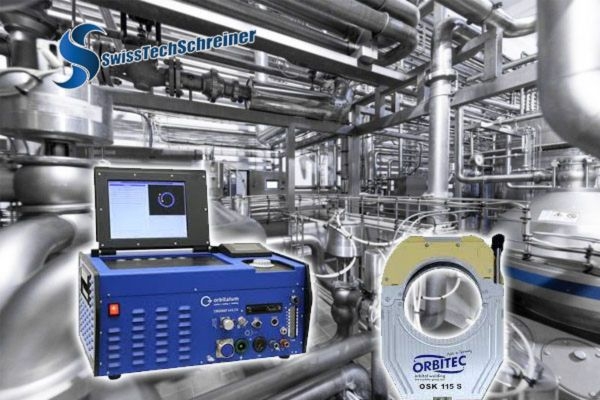
Bước Tiến Không Thể Thiếu Trong Chuỗi Sản Xuất Đồ Uống ( Beverage Industry)
Trong môi trường cạnh tranh ngày càng khốc liệt, yếu tố chất lượng và an toàn thực phẩm là "vũ khí" để các thương hiệu khẳng định giá trị. Việc đầu tư vào công nghệ orbital welding không chỉ nâng tầm quy trình sản xuất mà còn là sự cam kết mạnh mẽ với người tiêu dùng.
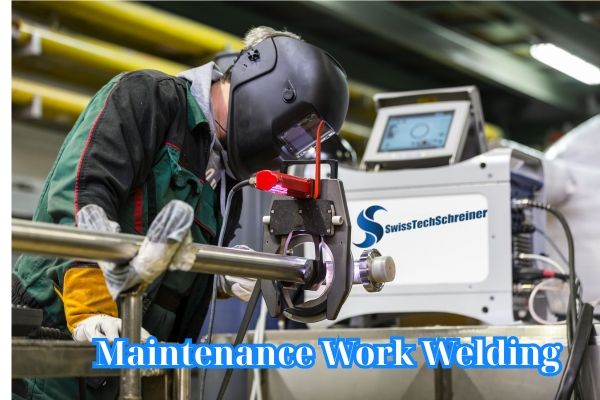
Maintenance Work Welding – Bảo Trì Hàn Hiệu Quả Cho Mọi Công Trình Kim Loại
Trong lĩnh vực công nghiệp hiện đại, việc duy trì độ bền và sự ổn định của các kết cấu kim loại đóng vai trò cực kỳ quan trọng. Một trong những giải pháp tối ưu nhất hiện nay chính là Maintenance Work Welding – dịch vụ bảo trì hàn chuyên sâu, giúp kiểm soát chất lượng công trình và kéo dài tuổi thọ thiết bị.
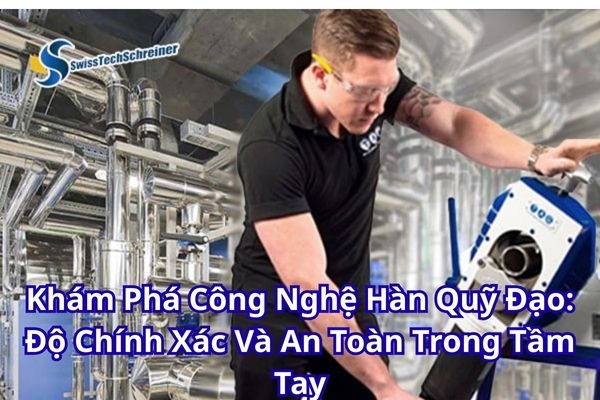
Khám Phá Công Nghệ Hàn Quỹ Đạo: Độ Chính Xác Và An Toàn Trong Tầm Tay - Orbital welding technology
Công nghệ hàn quỹ đạo (Orbital Welding Technology) đang trở thành lựa chọn hàng đầu trong nhiều ngành công nghiệp. Từ thực phẩm – đồ uống, dược phẩm đến hàng không – vũ trụ, phương pháp hàn này mang lại giải pháp tối ưu