Pipe welding is a crucial process in the construction and maintenance of various industries such as oil and gas, chemical, and power generation. It involves joining two or more pipes together to create a continuous flow of fluids or gases. In the past, pipe welding was done manually, which required skilled welders and was time-consuming. However, with the advancement of technology, the use of orbital welding machines has revolutionized the pipe welding process. This Swisstech Schreiner’s blog post will discuss the pipe welding technique using an orbital welding machine for achieving high-quality welds.
Preparing the Welding Workpiece
Before starting the welding process by orbital welding machine, it is essential to prepare the welding workpiece properly. This step is crucial as it ensures that the final weld is strong, durable, and free from defects. The following are the steps involved in preparing the welding workpiece:
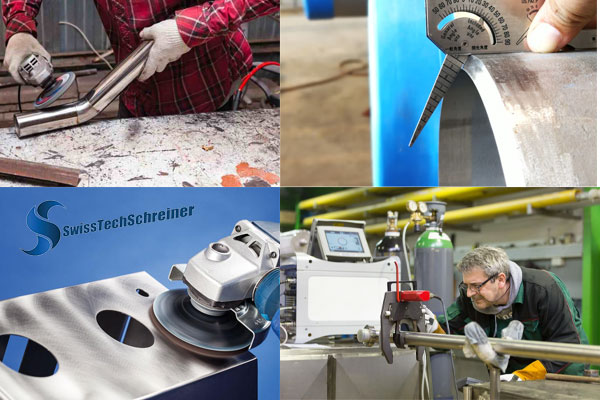
Cleaning the Surface
The first step in preparing the welding workpiece is to clean the surface of the pipes. Any dirt, oil, or rust on the surface can affect the quality of the weld. Therefore, it is necessary to remove any contaminants by using a wire brush, sandpaper, or chemical cleaners. The cleaning method used will depend on the type of material being welded. For instance, stainless steel pipes require a different cleaning method than carbon steel pipes.
Beveling the Edges
Beveling is the process of cutting or grinding the edges of the pipes to create a V-shaped groove. This groove allows for better penetration of the weld and creates a stronger joint. The bevel angle and width will depend on the thickness and diameter of the pipes. It is crucial to ensure that the bevel is uniform and free from any defects.
Aligning the Pipes
Proper alignment of the pipes is crucial for achieving high-quality welds. Misalignment can result in uneven welds, which can lead to leaks or cracks in the future. The pipes should be aligned using clamps or tack welds before starting the welding process orbital welding machine . This step is especially important when welding large diameter pipes.
Setting Up the Orbital Welding Machine
Once the welding workpiece is prepared, the next step is to set up the orbital welding machine. This machine is designed to rotate around the pipe while simultaneously welding it. The following are the steps involved in setting up the orbital welding machine:
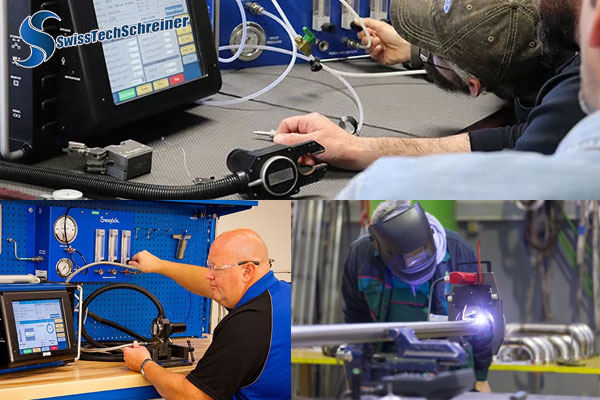
Choosing the Right Electrode and Gas
The first step in setting up the orbital welding machine is to select the appropriate electrode and gas for the type of material being welded. The electrode is the filler metal used to create the weld, while the gas is used to protect the weld from atmospheric contamination. The type of electrode and gas used will depend on the material being welded and the welding process.
Adjusting the Welding Parameters
The next step is to adjust the welding parameters on the orbital welding machine. These parameters include voltage, amperage, travel speed, and rotation speed. It is essential to follow the manufacturer's recommendations for the specific material being welded to achieve the desired weld quality. The welding parameters can also be adjusted during the welding process to ensure consistent and uniform welds.
Positioning the Weld Head
The weld head is the part of the orbital welding machine that holds the electrode and rotates around the pipe. It is crucial to position the weld head correctly to ensure proper alignment with the joint. The weld head should be positioned at a 90-degree angle to the joint and centered on the pipe. This step is critical for achieving a symmetrical and uniform weld.
The orbital welding machine's pipe welding process is a highly efficient and precise method utilized in various industries for welding pipes with a high level of accuracy and repeatability. This advanced welding technique involves mounting the welding head onto the pipe and allowing it to rotate around the pipe while simultaneously welding. The orbital welding machine ensures uniformity in the weld bead, minimizing the chances of defects and ensuring a high-quality weld.
This process is particularly beneficial in industries where the integrity of welded joints is crucial, such as aerospace, pharmaceuticals, and the food and beverage industry. The automated nature of orbital welding reduces the need for manual intervention, resulting in increased productivity and consistency in weld quality. Additionally, the use of inert gas shielding during orbital welding helps prevent oxidation and contamination of the weld, further enhancing the integrity of the welded joint. Overall, the orbital welding machine's pipe welding process is a cutting-edge technology that delivers precision, reliability, and efficiency in the fabrication of high-quality welded pipes.
Tips for Achieving High-Quality Welds with Orbital Welding Machine in Pipe Welding
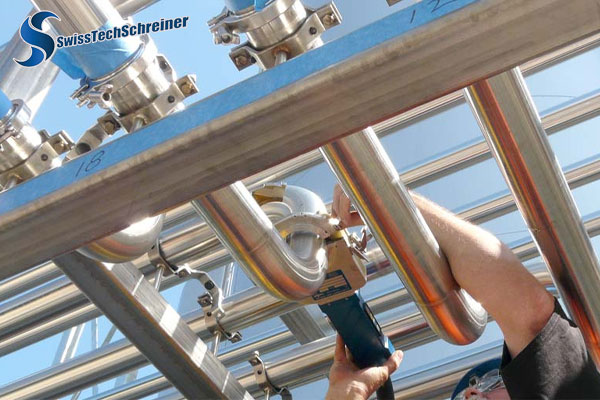
The following are some tips for achieving high-quality welds when using an orbital welding machine in pipe welding:
- Proper preparation of the welding workpiece is crucial for achieving high-quality welds. This includes cleaning the surface, beveling the edges, and aligning the pipes.
- It is essential to choose the right electrode and gas for the type of material being welded.
- Adjusting the welding parameters according to the manufacturer's recommendations is crucial for achieving consistent and uniform welds.
- Tack welding should be done using the same process and parameters as the final weld.
- The buffer layer is essential for achieving high-quality welds, especially when welding dissimilar materials.
- Creating the keyhole opening at the top of the weld pool allows for better penetration and fusion between the base metal and the filler metal.
- Regular inspection of the welds during the welding process is crucial for identifying and repairing any defects.
- Proper training and certification of welders is necessary for ensuring the quality and safety of the welding process.
=> Read more at :
=> Components and Features of an Orbital Welding Machine
=> Reasons why orbital welding machines are suitable for pipe welding
=> Services related to Orbital Welding Machine
Conclusion
In conclusion, the use of orbital welding machines has revolutionized the pipe welding process, making it faster, more efficient, and producing higher quality welds. With the continuous advancements in technology, the future of pipe welding using orbital welding machines looks promising, with even more precise and efficient techniques being developed. Please contact Swiss Tech Schreiner if your business needs help with pipeline construction solutions, orbital welding, plant maintenance,...
Swisstech Schreiner.
Add: ch 4153 reinach and hcm city vietnam
Hotline: (+84) 931 - 386 - 062
Phone: (+84) 931 - 386 - 062 +84931386062 ( zalo / viber / whatsapp )
Email: swiss.tech.schreiner@gmail.com
Other News
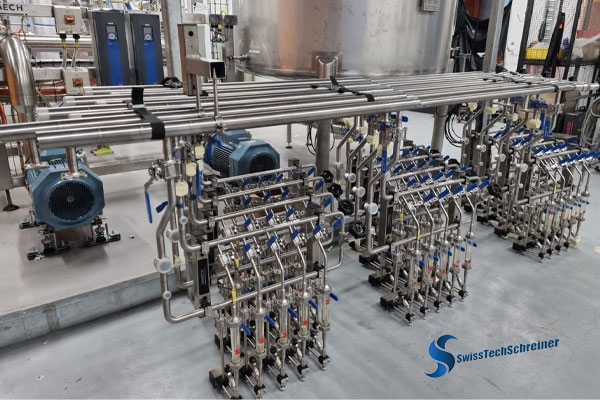
Công nghệ hàn quỹ đạo orbital welding technology phòng sạch
Công nghệ hàn quỹ đạo orbital welding technology trong phòng sạch ứng dụng cho nhiều nhà máy dược phẩm, vi sinh. Bài viết này của Swisstech Schreiner sẽ đi sâu vào các yêu cầu này để doanh nghiệp có cái nhìn chi tiết về chất lượng hàn.
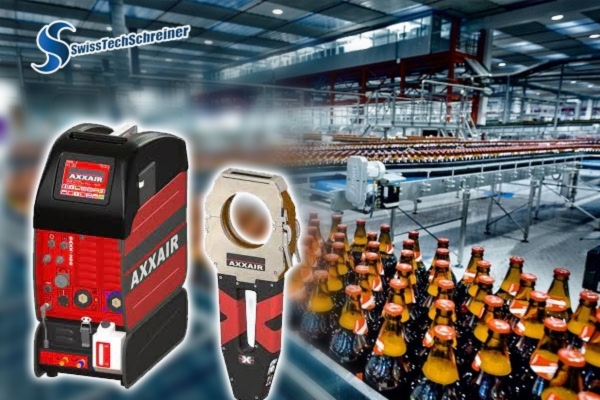
SwissTech Schreiner – Hàn Quỹ Đạo Tối Ưu Cho Ngành Nước Giải Khát
Trong các dây chuyền sản xuất nước giải khát, hệ thống ống dẫn đóng vai trò quan trọng trong việc vận chuyển nguyên liệu và sản phẩm. Việc sử dụng ống thép không gỉ vi sinh cùng công nghệ hàn quỹ đạo là lựa chọn tối ưu để đảm bảo
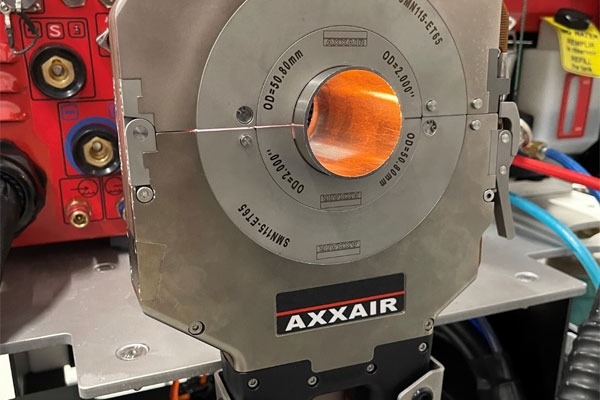
Tầm Quan Trọng Của Bảo Dưỡng Máy Hàn
Bảo trì máy hàn quỹ đạo định kỳ giúp đảm bảo hiệu suất ổn định, kéo dài tuổi thọ thiết bị và ngăn ngừa sự cố. Tìm hiểu ngay lý do bảo trì là yếu tố không thể thiếu để tối ưu hóa chất lượng và an toàn trong sản xuất!

Dịch vụ bảo dưỡng thiết bị công nghiệp chuyên nghiệp
Swisstech Schreiner cung cấp dịch vụ bảo dưỡng thiết bị công nghiệp chuyên nghiệp, định kỳ theo tháng, quý, năm giúp nhà máy duy trì hoạt động ổn định, tăng tuổi thọ máy móc và giảm thiểu sự cố phát sinh.
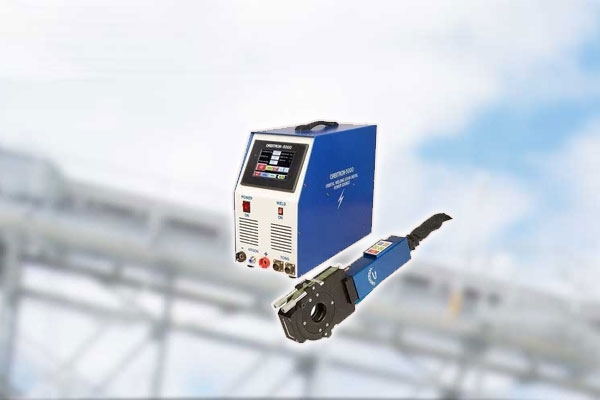
Quy trình hàn quỹ đạo trong ngành đồ uống (beverage industry)
Khám phá lợi ích của công nghệ hàn quỹ đạo trong ngành đồ uống beverage industry : đảm bảo vệ sinh an toàn thực phẩm, mối hàn bền chắc, quy trình tự động hóa hiệu quả, giúp nâng cao chất lượng sản phẩm và tối ưu hóa sản xuất.
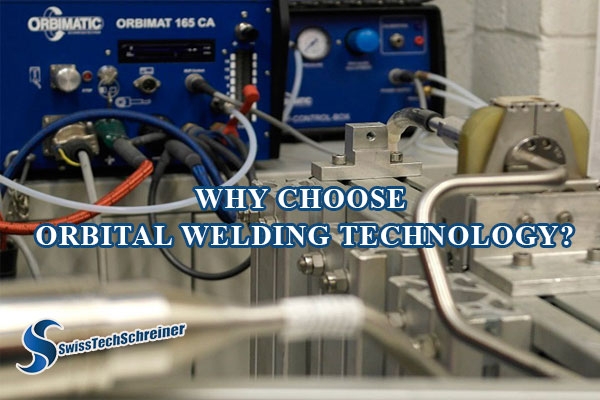
Why Choose Orbital Welding Technology?
The advent of orbital welding technology has changed the landscape of welding industries, from aerospace to orbital pharmaceutical and beyond. Let's explore orbital welding technology more deeply with Swisstech Schreiner through the following article