In the fast-evolving world of industrial construction, efficiency and precision are paramount. Orbital welding technology has become one of the most popular technologies in the field of construction of clean biological pipeline systems . With its unmatched accuracy and consistency, this cutting-edge tool has become indispensable for projects demanding the utmost quality. Let's learn about this welding technology with Swisstech Schreiner through the following article
Orbital welding technology comes from AXXAIR
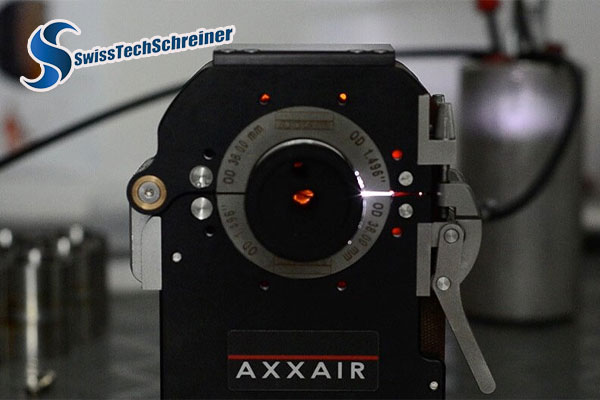
Orbital welding technology has redefined efficiency and precision in the attachment of tubes to tube sheets. This advanced technique not only accelerates the welding process but also enhances the quality of the welds significantly. AXXAIR stands at the forefront of this innovation, integrating orbital welding with specialized features designed for seamless operation and superior results.
This orbital welding machine is an inclined electrode and water-cooled heads, essential for maintaining the integrity of the welds by preventing overheating, especially during prolonged cycles that are a norm in such applications. Additionally, the wire spool’s design ensures a firm mount, eliminating the risk of misalignment due to wire twisting.
AXXAIR's commitment to convenience and efficiency extends to the user-friendly interface, allowing operators to initiate the welding cycle right from the handle, which is a boon for productivity given that the control station is often a distance away. This meticulous approach to orbital welding technology not only streamlines the construction of heat exchangers but also ensures each weld is documented for traceability, upholding the highest standards of quality and accountability in the process.
Note when using orbital welding machine
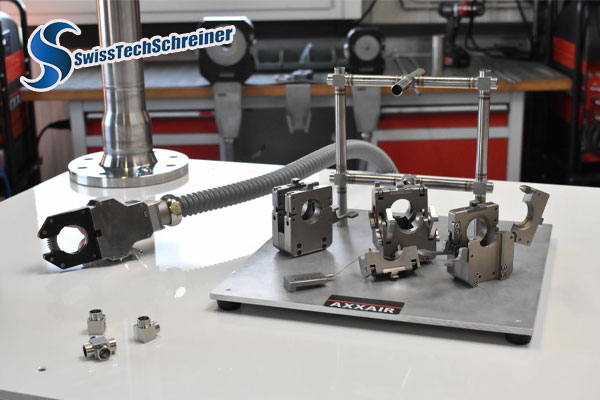
Navigating the intricacies of tube-to-tube-sheet welding demands a deep understanding of the preparation and geometric intricacies of the tube assembly. AXXAIR stands as a beacon of guidance in this specialized field, offering orbital welding technology and machines designed to handle these complex configurations with precision.
While AXXAIR's expertise is a valuable resource, the onus of welding outcomes rests with the customers. They hold the reins when it comes to deciding on the preparation and positioning of the tubes within the tube sheets—a decision that crucially influences the quality of the final weld.
The scope of materials that can be welded with orbital welding technology is broad, accommodating a variety of tube dimensions predominantly found in the chemical, food and beverage industry, biological and pharmaceutical sector where heat exchangers are essential.
These dimensions typically span diameters of 12.7 to 101.6 mm with thicknesses ranging from 0.5 to 5 mm. However, it's the tubes ranging from 19.05 mm to 38.1 mm in diameter and 1.65 to 3.4 mm in thickness that are most commonly employed. This meticulous process underscores the symbiosis between AXXAIR's innovative solutions and the strategic choices made by clients, ensuring the seamless operation of industries that rely on these critical heat exchangers.
=> Read more at :
=> Orbital Welding technology - automatic welding machine service
=> Advantages and Disadvantages Of Orbital Welding Technology
=> The Beverage Industry’s Embrace of Orbital Welding Technology
General characteristics When applying orbital welding technology
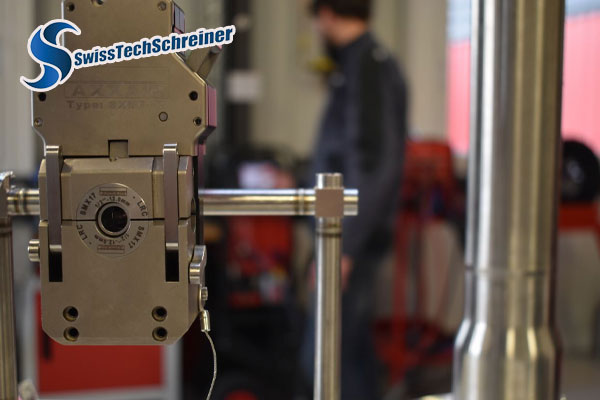
When it comes to orbital welding technology, the choice of equipment is pivotal and varies with the application's complexity and the degree of automation desired. For instance, welding titanium tubes requires a standard orbital welding setup that includes a power supply and a specialized welding head with a protective gas chamber. If the task calls for the addition of filler wire, the power supply and welding head are upgraded to facilitate wire feeding, making them suitable for single pass welding jobs.
However, for double pass applications, this standard orbital welding machine may need manual adjustments of the electrode between passes. While more sophisticated welding heads exist—capable of automatic electrode adjustments to perform dual passes seamlessly and equipped with AVC/OSC capabilities for highly specialized tasks—such advanced features are not currently within AXXAIR's product offerings. This delineation underscores the importance of selecting the right equipment for the job, a decision that directly affects the efficacy and outcome of the welding process in various industrial applications.
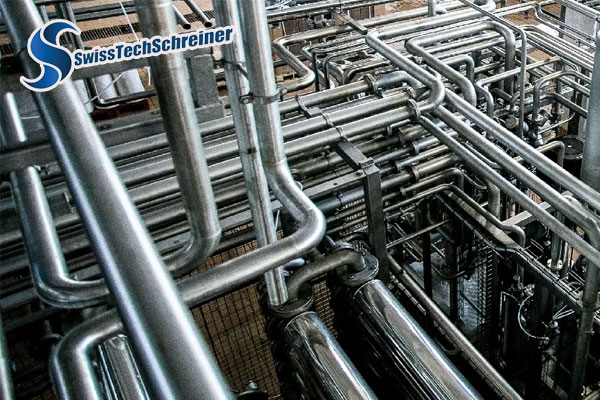
Please note: Ensuring the precision of orbital welding technology begins with the proper positioning of the tubes within the tube sheets—a task that may require specific centering tools compatible with AXXAIR's design standards. It's crucial that the interface where the tube meets the tube sheet is impeccably clean, devoid of grease, oil, or any contaminants that could lead to imperfections, such as bubbles in the weld bead. Moreover, pre-expansion of the tubes in the tube sheet must be avoided. This step is critical because any gases trapped during the welding process can lead to pressure build-up, risking a disruptive "explosion" that would render automatic welding infeasible. This guidance is vital for maintaining the integrity of the weld and for the seamless execution of the welding operation.
In the realm of pipeline construction, the orbital welding device stands as a beacon of modern engineering, offering unparalleled precision and reliability. This sophisticated piece of machinery has been tailored to meet the high standards of today's construction projects, where the margin for error is negligible and the demands for quality are towering. Embracing the power of automation, orbital welding machines provide a consistent output that manual welding could never match, ensuring uniformity and strength across countless welds.
The technological prowess of these machines shines through in their ability to tackle complex welding geometries with ease, adapting to a variety of pipeline configurations. Moreover, the integration of advanced features such as programmable weld schedules, real-time monitoring, and detailed weld documentation takes quality control to new heights, instilling confidence in the integrity of each joint.
As the industry progresses, the adoption of orbital welding technology has become a cornerstone in the construction of pipelines, guaranteeing not just speed and efficiency, but also the safety and longevity of the infrastructure being laid down. For contractors and clients alike, the investment in an orbital welding machine translates into cost savings, reduced downtime, and a significant edge in a competitive market.
In essence, the fusion of innovation and practicality that orbital welding machines embody marks a significant leap forward in pipeline construction, setting new benchmarks for the industry's future. Contact Swisstech Schreiner if you need more detailed information about orbital welding products, or solutions when building industrial pipelines, or need training on orbital welding technology at the the following contact information.
Swisstech Schreiner.
Add: ch 4153 reinach and hcm city vietnam
Hotline: (+84) 931 - 386 - 062
Phone: (+84) 931 - 386 - 062 +84931386062 ( zalo / viber / whatsapp )
Email: swiss.tech.schreiner@gmail.com
Other News
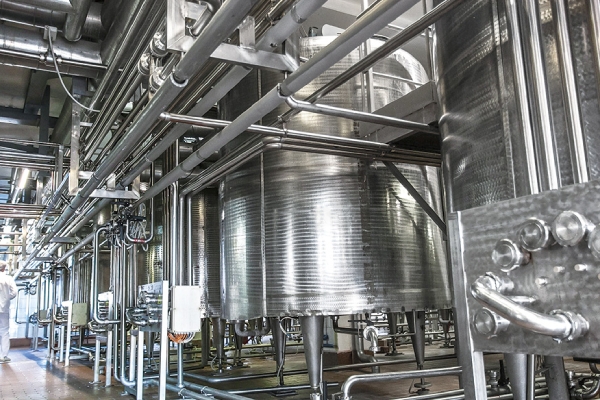
Gia công ống thép không gỉ bằng công nghệ hàn quỹ đạo
Hàn quỹ đạo – Giải pháp tối ưu gia công ống thép không gỉ với độ chính xác cao, tiết kiệm chi phí và đảm bảo chất lượng. Liên hệ Swisstech Schreiner ngay để nhận tư vấn các giải pháp hợp lý.
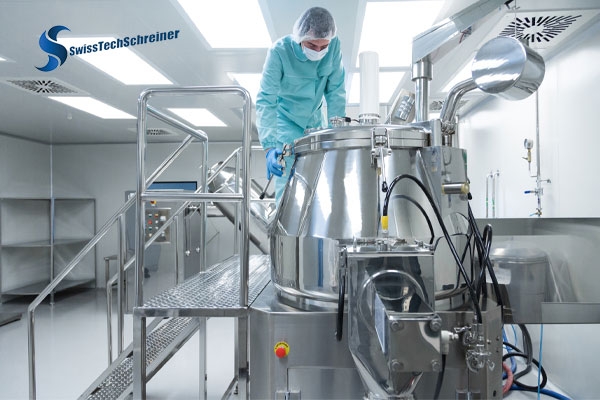
Lý Do Tại Sao Hàn Orbital Được Tin Dùng Trong Ngành Sữa
Ngày nay, hàn công nghệ quỹ đạo orbital welding technology đang trở thành xu hướng nổi bật trong nhiều ngành công nghiệp, đặc biệt là trong ngành sản xuất sữa. Hãy cùng tìm hiểu thêm chi tiết về công nghệ hàn thông qua bài sau.
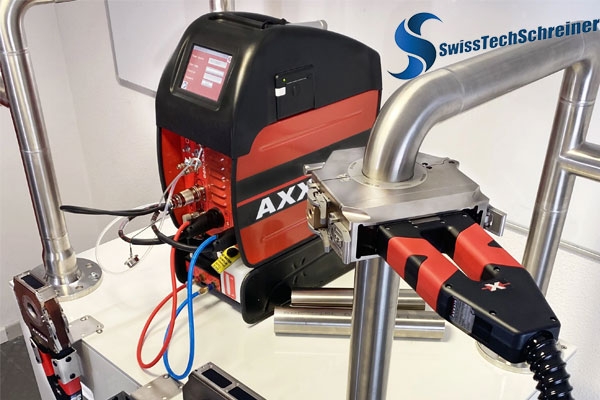
TIG Orbital Welding Machine - Thiết bị hàn quỹ đạo TIG
Giải pháp đặt ra cho nhiều ngành công nghiệp đòi hỏi khắt khe về nhu cầu hàn đó là tự động hóa quy trình hàn ống dẫn trong hệ thống đường ống bằng công nghệ với thiết bị hàn quỹ đạo (orbital welding machine). Hệ thống hàn TIG quỹ đạo (TIG Orbital Welding Machine) tự động hóa các khía cạnh khó khăn nhất của quy trình hàn, cho phép người vận hành tập trung vào việc mang lại kết quả chất lượng.
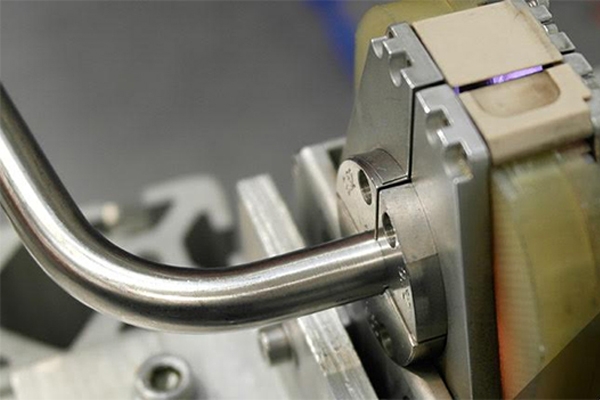
Vì sao nên gia công ống thép không gỉ (Stainless steel pipe processing) bằng máy hàn quỹ đạo?
Tại sao nên sử dụng máy hàn quỹ đạo trong quá trình gia công thép không gỉ (Stainless steel pipe processing)? Hãy cùng Swisstech Schreiner tìm hiểu gia công thép không gỉ là gì? Máy hàn quỹ đạo là gì? Và những lợi ích khi gia công thép không gỉ bằng máy hàn quỹ đạo tại ở bài viết sau nhé.
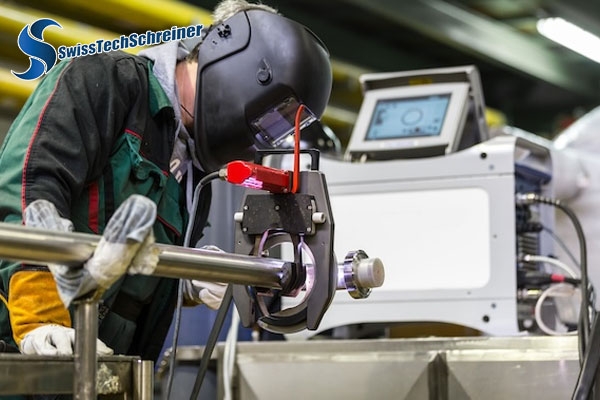
Công Nghệ Hàn Quỹ Đạo Orbital Cho Ống Inox Vi Sinh Và Công Nghiệp
Công nghệ hàn quỹ đạo hay còn gọi là hàn orbital, đây là công nghệ hàn được sử dụng rộng rãi, mang lại các mối hàn nhất quán, chất lượng cao và thượng được các nhà thầu thi công đường ống vi sinh sử dụng.
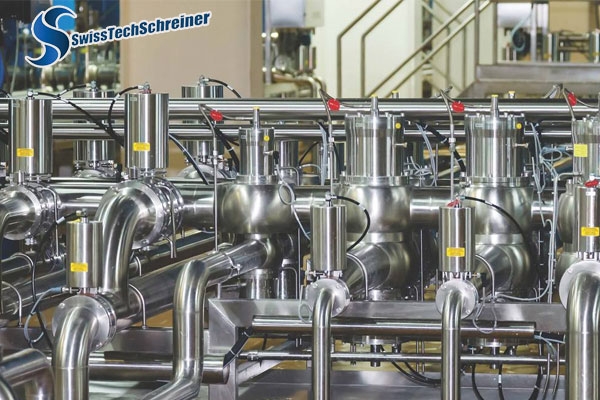
The Orbital Welding Technology in the Beverage Industry: Revolutionizing Quality and Efficiency
Discover how orbital welding technology is transforming the beverage industry, revolutionizing production quality and efficiency. Let's at Swisstech Schreiner explore the techniques and innovations that are raising the bar for beverage manufacturing in this exploration of orbital welding's impact.