This article delves into the nuanced world of orbital welding technology, laying out its myriad advantages that have made it an indispensable tool in sectors like aerospace, pharmaceuticals, and semiconductor manufacturing, while also navigating the disadvantages that businesses must consider. Join Swisstech Schreiner as we explore the intricate dance of pros and cons that orbit around this futuristic welding technology.
Which industries apply orbital welding technology?
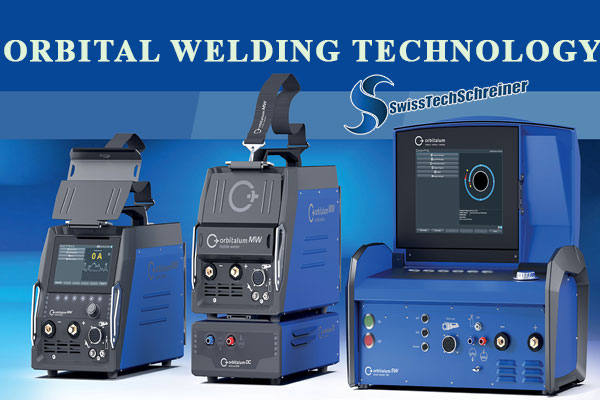
Orbital welding technology stands as a pinnacle of precision and consistency in various industries where the integrity of welds is non-negotiable. This advanced technique utilizes computer-controlled processes to achieve high-quality welds around the circumference of pipes and tubes, a critical function in sectors that demand utmost safety and reliability.
Within the aerospace industry, orbital welding is indispensable; it ensures the structural soundness of aircraft and spacecraft, where every joint and seam must withstand extreme pressures and temperatures. The pharmaceutical industry also relies heavily on this technology to maintain the purity and hygiene of their process piping.
Similarly, the semiconductor industry, where even the slightest impurities or variations can compromise the production of microchips, embraces orbital welding for its ability to create uncontaminated and precise welds. In the food and beverage industry, the durability and leak-tightness of welds achieved through orbital welding technology are critical to maintaining operational safety and regulatory compliance.
By integrating orbital welding machine in these industries, industries benefit from the repeatability and efficiency it brings to their operations, marking orbital welding as a key player in their pursuit of excellence.
Orbital welding technology, a specialized area of welding that demands precision and control, has revolutionized pipe and tube joining processes across various industries. Its surge in popularity is no accident; the method boasts enhanced weld consistency, superior quality, and improved safety, positioning it as a cornerstone in operations that cannot compromise on the exactness of their welds. However, as with any technological advancement, it presents its own set of challenges. The initial costs and the need for skilled operators can act as potential barriers to its widespread adoption.
Advantages Of Orbital Welding Technology
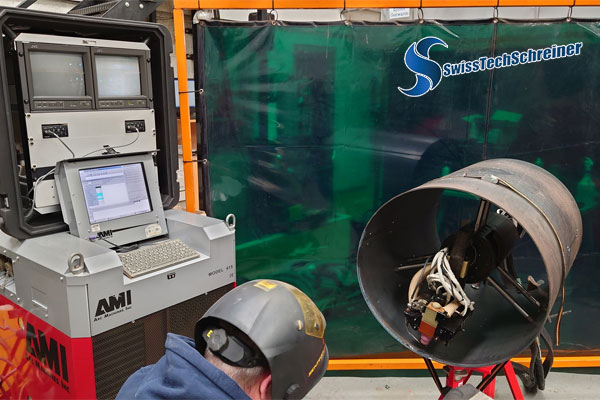
In the realm of modern fabrication, orbital welding technology emerges as a game-changer, revolutionizing the way industries approach joining metals. This innovative method brings forth a suite of advantages that cater to the high demands of precision, efficiency, and strength required in today's competitive landscape. With its automated process, orbital welding technology significantly reduces the margin for human error, delivering consistent, high-quality welds that are repeatable across multiple applications.
The enhanced precision not only augments the aesthetic appeal of the welds but also plays a pivotal role in industries where exactitude is critical, such as in the alignment of pipelines in oil and gas sectors or the delicate assemblies in the aerospace field. Orbital welding machine capacity to operate in environments that are challenging for manual welders—like confined spaces or hazardous conditions—further underscores its value.
Moreover, the speed with which orbital welding machines complete welds translates into reduced labor costs and faster project turnarounds, making it a financially sound investment. In essence, orbital welding technology represents a sophisticated fusion of technology and craftsmanship, driving industries forward with its unmatched advantages in both quality and operational efficiency.
Disadvantages Of Orbital Welding Technology
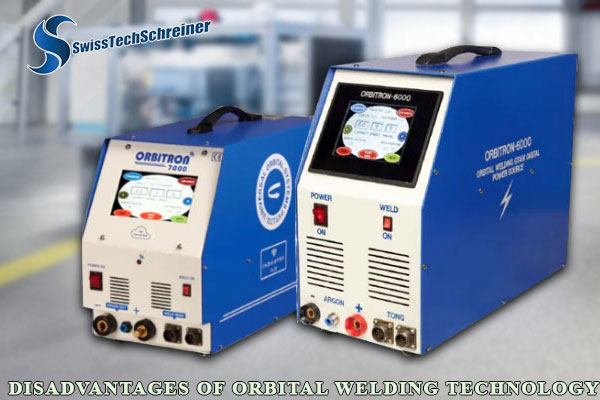
While orbital welding technology stands as a beacon of innovation in the manufacturing landscape, it's important to recognize that it's not without its challenges. As industries worldwide increasingly integrate this technology into their operations, they also grapple with its complexities. The initial investment in orbital welding machines can be substantial, presenting a financial hurdle for smaller operations. The sophisticated nature of the machinery requires operators to have specialized training, creating a steeper learning curve and potentially leading to a scarcity of qualified technicians.
Moreover, the very precision of orbital welding machine, while beneficial, also leaves little room for error; even minor mis-calibrations can result in costly project setbacks. The technology's reliance on electricity and programming also means that it can be more susceptible to technical malfunctions compared to more traditional welding methods, requiring a higher standard of maintenance and backup solutions in case of system failures. Despite these considerations, the future of orbital welding technology remains bright, as continuous advancements aim to mitigate these disadvantages, ensuring its place as a cornerstone in the evolution of fabrication.
=> Read more at :
=> Considerations for Orbital Welding Technology in BioProcess Piping Application
=> The Beverage Industry’s Embrace of Orbital Welding Technology
=> Orbital Welding Technology for Pipeline Systems Construction
Orbital welding technology in the application of microbial pipeline construction at Swisstech
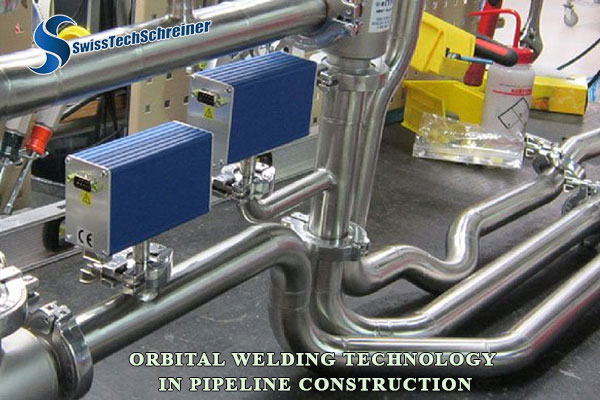
Orbital welding technology has become the cornerstone of precision in pipeline construction at Swisstech, setting a new benchmark in the creation of microbial pipelines. This cutting-edge approach to welding has enabled Swisstech to construct pipelines that meet the stringent standards required for microbial applications. By employing this advanced technology, Swisstech ensures that each weld is of the highest quality, boasting uniformity and strength that manual welding processes could hardly match. The importance of such precision cannot be overstated in microbial pipelines, where even the slightest imperfection can become a breeding ground for contamination.
Swisstech's adoption of orbital welding technology reflects their commitment to excellence and innovation. It allows for the meticulous control of welding variables in real-time, ensuring optimal conditions for each weld, which is crucial in environments that must be kept free from microbial contamination. Moreover, the technology's ability to consistently produce clean, strong, and penetration-controlled welds addresses the critical need for uncontaminated fluid flow in microbial pipelines.
The application of orbital welding technology at Swisstech has not only enhanced the integrity of their microbial pipelines but also resulted in increased efficiency, reducing construction time and costs while upholding the highest quality standards. It's a harmonious blend of technology and expertise that positions Swisstech at the forefront of the biotechnological industry, marking a significant leap in the way microbial pipelines are constructed. As Swisstech continues to harness the potential of orbital welding, they pave the way for safer and more reliable microbial applications, reinforcing their role as a leader in the field
Swisstech Schreiner.
Add: ch 4153 reinach and hcm city vietnam
Hotline: (+84) 931 - 386 - 062
Phone: (+84) 931 - 386 - 062 +84931386062 ( zalo / viber / whatsapp )
Email: swiss.tech.schreiner@gmail.com
Other News
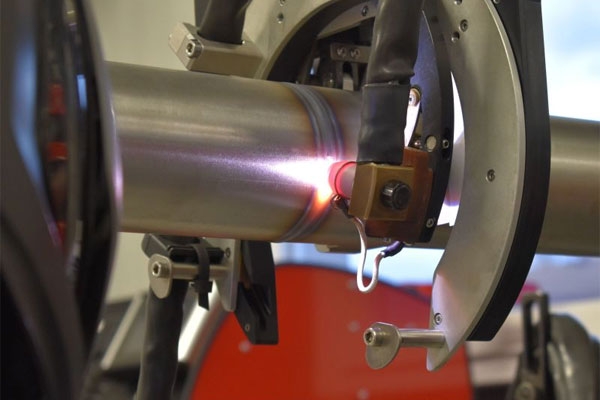
Ứng dụng và lợi ích của máy hàn quỹ đạo trong kỹ thuật đường ống
Tìm hiểu ứng dụng và lợi ích của máy hàn quỹ đạo Orbital welding machine trong kỹ thuật đường ống. Khám phá nguyên lý hoạt động, ưu điểm vượt trội và các ứng dụng thực tiễn trong lắp đặt, bảo trì và chế tạo đường ống cho các ngành thực phẩm, đồ uống, dược phẩm.
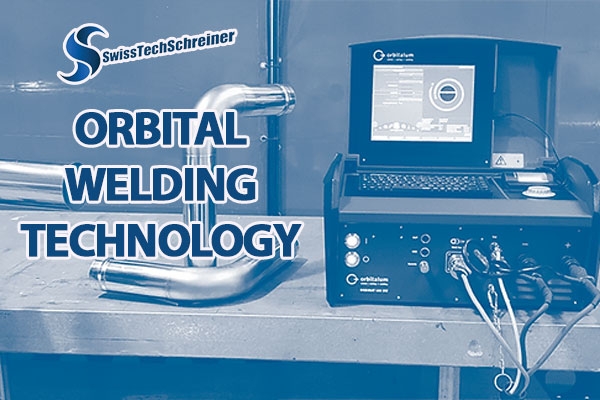
Orbital Welding technology - automatic welding machine service
Do you need to rent, buy, train or modify an orbital welding machine or orbital welding technology services ? Contact our hotline: (+84) 931 - 386 - 062 or swiss.tech.schreiner@gmail.com for detailed information. Or you can fill out the form below to let Swisstech Schreiner know your request.
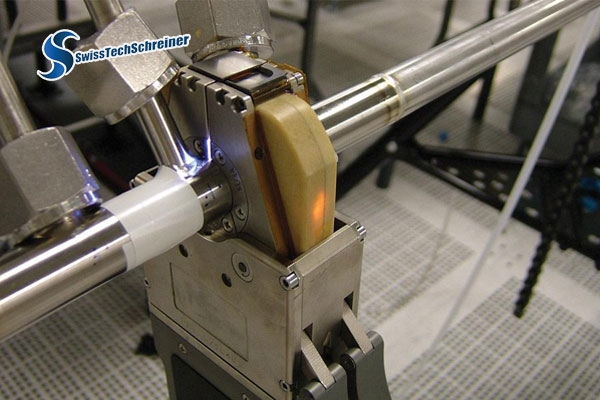
Swisstech Schreiner provides the solution for Stainless Steel Pipe Processing With Orbital Welding technology
Join Swisstech Schreiner in embracing a new era of stainless steel pipe processing, where technology meets ingenuity. Swisstech Schreiner's dedication to innovation continues to reshape possibilities and elevate industry standards. Experience the future of welding – precise, efficient, and flawlessly connected.
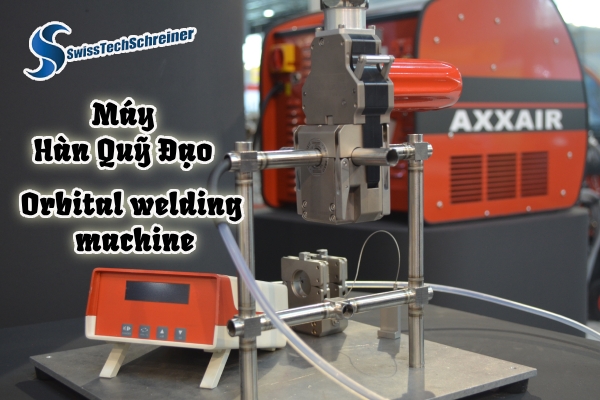
Kỹ thuật sử dụng máy hàn quỹ đạo Orbital welding machine cho mối hàn hoàn hảo
Máy hàn quỹ đạo Orbital welding machine là một trong những công nghệ hàn hiện đại và tiên tiến nhất hiện nay. Trong bài viết này, hãy cùng Swiss Tech Schreiner sẽ cùng tìm hiểu về kỹ thuật sử dụng máy hàn quỹ đạo Orbital welding machine cho mối hàn hoàn hảo.
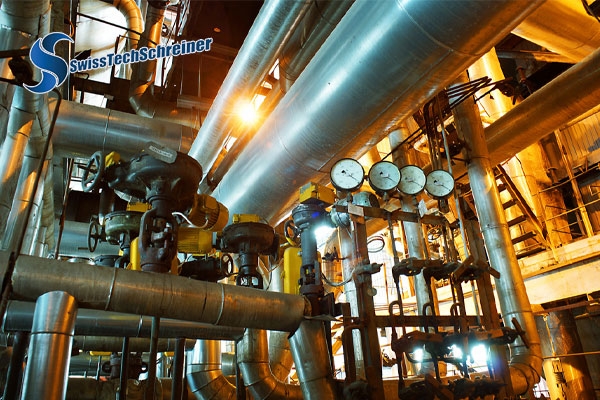
Sửa chữa mối hàn: Phân loại, quy trình và những lưu ý quan trọng
Sửa chữa mối hàn Maintenance work welding là một phần không thể thiếu trong các ngành công nghiệp liên quan đến sản xuất và bảo trì thiết bị. Bài viết dưới đây của Swisstech Schreiner sẽ cung cấp cái nhìn toàn diện về các loại sửa chữa mối hàn, phương pháp thực hiện và những lưu ý quan trọng trước khi tiến hành.
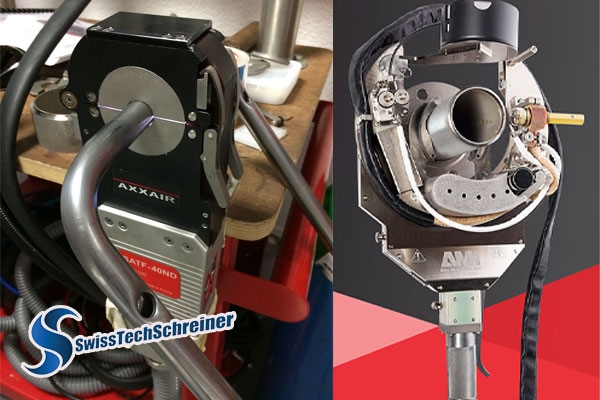
Orbital welding technology applied to industrial pipeline construction
With its unmatched accuracy and consistency, this cutting-edge tool has become indispensable for projects demanding the utmost quality. Let's learn about orbital welding technology with Swisstech Schreiner through the following article