Orbital welding technology stands at the forefront of precision and efficiency in the welding industry. This article delves into the intricate world of orbital welding, uncovering the various techniques that have revolutionized pipeline construction, food and beverage industry, and numerous other sectors requiring impeccable welds. Join Swisstech Schreiner on this journey through the high-tech world of orbital welding, where precision meets innovation.
Preparation Is the Greatest Welding Technique
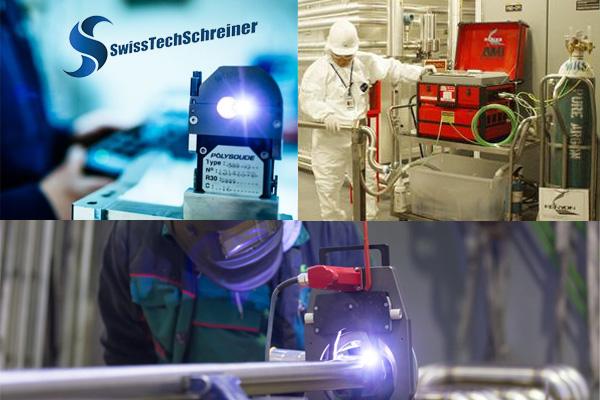
In the realm of orbital welding technology, preparation emerges as the linchpin for unparalleled success. This technique, often overshadowed by the allure of advanced machinery and innovative software, holds the key to precision and excellence in welding projects. By focusing on meticulous preparation, welders can ensure that every joint, every seam, and every weld is executed with the highest level of accuracy and strength. Such diligence in preparation not only enhances the quality of the final product but also elevates the efficiency and reliability of the welding process.
This approach aligns perfectly with the demands of industries where orbital welding technology is critical, such as aerospace, pharmaceuticals, and petrochemicals, where even the slightest imperfection can have significant consequences. By championing preparation as the greatest technique in orbital welding, we embrace a philosophy that prioritizes attention to detail, thoroughness, and a deep understanding of materials and orbital welding machines, setting a new standard of excellence in the field.
Different Welding Techniques Used in Orbital Welding Technology
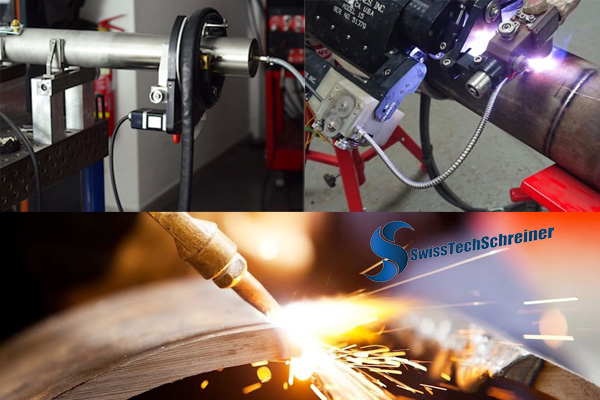
Orbital welding technology, a cornerstone in modern fabrication, employs a diverse array of welding techniques, each tailored to meet the unique demands of various industries. This versatility is a testament to the innovation and adaptability inherent in the field. Among these techniques, Tungsten Inert Gas (TIG) welding stands out for its precision and cleanliness, making it ideal for high-purity applications like pharmaceuticals and semiconductor manufacturing. On the other hand, Metal Inert Gas (MIG) welding offers speed and efficiency, favored in sectors where time is of the essence.
Another notable technique is Plasma Arc Welding, which excels in penetrating thick materials, a go-to method in aerospace and heavy industry. These techniques not only highlight the technical proficiency required in orbital welding but also underscore the technology's commitment to providing solutions that are both high-quality and cost-effective. As we delve into the intricacies of each method, it becomes evident that the choice of technique in orbital welding is not just a matter of preference but a strategic decision, driven by the specific needs of the project at hand. This multifaceted approach cements orbital welding technology's role as a key player in the ever-evolving landscape of industrial fabrication.
Different Welding Techniques for Different Welding Positions
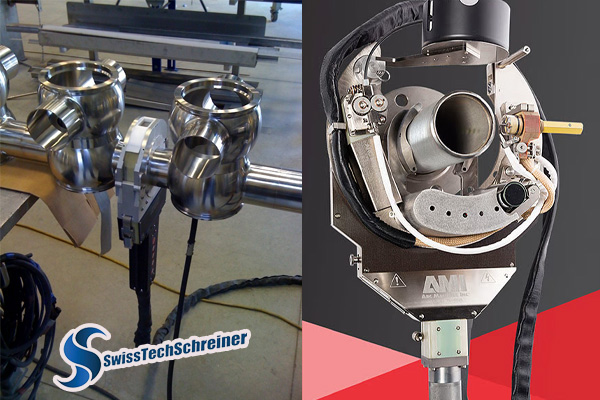
The art of welding is as varied as the positions in which welds are executed, with each technique offering unique benefits tailored to specific orientations. For flat or horizontal welding, Shielded Metal Arc Welding (SMAW) is often the go-to choice, known for its versatility and ease of use in creating strong, durable joints. When tackling overhead welding, Flux-Cored Arc Welding (FCAW) is preferred for its flux core wire that enhances the stability and quality of the weld in these challenging positions. Vertical welding, on the other hand, finds a perfect match in Gas Tungsten Arc Welding (GTAW), also known as TIG welding, which provides the precision and control needed for vertical seams.
Each of these techniques requires not only a deep understanding of the Orbital welding technology process but also an adaptation to the gravitational challenges and accessibility issues presented by different welding positions. This nuanced approach to welding positions ensures that the integrity of the weld is maintained, regardless of the orientation, making it a critical consideration in projects ranging from infrastructure development to automotive manufacturing. By mastering different welding techniques for various positions, welders can guarantee optimal outcomes, showcasing the adaptability and skill that define the welding profession.
=> See more articles on the same topic at :
=> (Orbital welding machine) Máy hàn quỹ đạo: giải pháp hiệu suất dành cho doanh nghiệp
=> TIG Orbital Welding Machine - Thiết bị hàn quỹ đạo TIG
=> Choosing the right pipe welding method?
The reasons for Deploying Orbital Welding for Different Welding Techniques
The deployment of Orbital welding technology in diverse welding techniques is a strategic choice driven by its unparalleled precision, consistency, and efficiency. This advanced technology is particularly indispensable in scenarios demanding high-quality welds, such as in the food and beverage industry, pharmaceutical, and petrochemical industries. One of the primary reasons for its widespread use is the ability of orbital welding to deliver uniform and repeatable welds, a necessity in applications where the slightest variation can lead to significant safety or quality concerns.
Additionally, orbital welding excels in environments where access is restricted or welds are in hard-to-reach areas, ensuring that even the most challenging joints are executed flawlessly. This technique also significantly reduces the likelihood of human error, enhancing the overall integrity of the welding project. Furthermore, the speed and efficiency offered by orbital welding machine mean that projects can be completed faster, without sacrificing quality, which is crucial in time-sensitive industries. By embracing orbital welding, companies are not just investing in a welding technique; they are investing in a guarantee of quality, safety, and efficiency, making it a cornerstone in modern fabrication and construction methodologies.
With this article, readers will gain insights into automated processes, the versatility of Orbital welding technology in different environments, and how this technology continually adapts to meet the ever-evolving demands of industry standards. Whether you're a seasoned professional or new to the world of welding, this blog offers a comprehensive guide to understanding the intricacies and applications of orbital welding techniques.
Swisstech Schreiner.
Add: ch 4153 reinach and hcm city vietnam
Hotline: (+84) 931 - 386 - 062
Phone: (+84) 931 - 386 - 062 +84931386062 ( zalo / viber / whatsapp )
Email: swiss.tech.schreiner@gmail.com
Other News
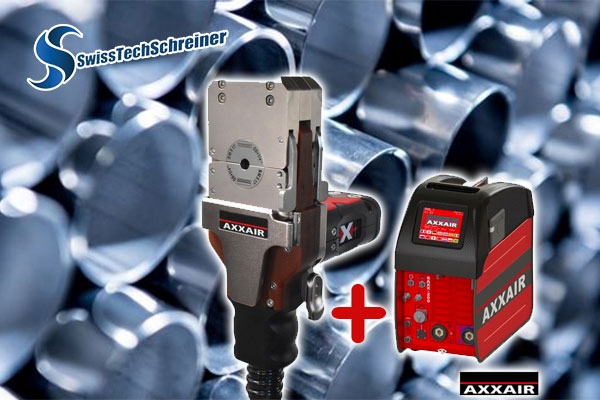
Mẹo hàn gia công ống thép không gỉ Stainless steel pipe processing
Khám phá các mẹo hàn gia công ống thép không gỉ Stainless steel pipe processing hiệu quả và nhanh chóng. Cùng Swisstech Schreiner tìm hiểu cách xử lý và cải thiện chất lượng mối hàn, giúp công trình của bạn bền vững hơn
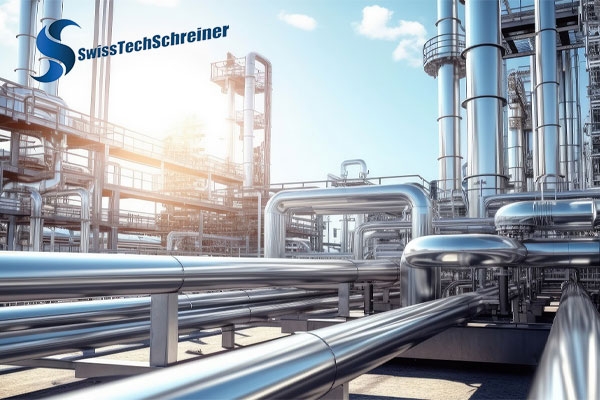
Hướng Dẫn Sửa Chữa Và Bảo Trì Hàn Maintenance Work Welding
Sửa chữa và bảo trì hàn Maintenance work welding là một quá trình quan trọng nhằm đảm bảo tạo ra các thành phần an toàn và có thể sử dụng được. Bài viết này của Swisstech Schreiner cung cấp thông tin về các hướng dẫn cơ bản cho quá trình sửa chữa hàn.
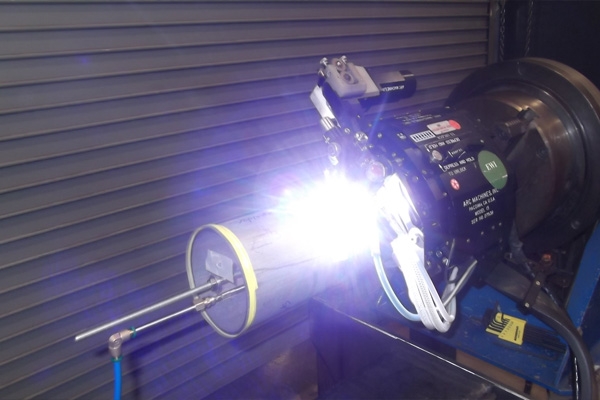
Orbital welding technology ‘s definition and history
New technologies require cleaner and more precise welds in industries such as the food and beverage industry, pharmaceutical industry. That is the reason why orbital welding technology appears and has become more popular in the world.
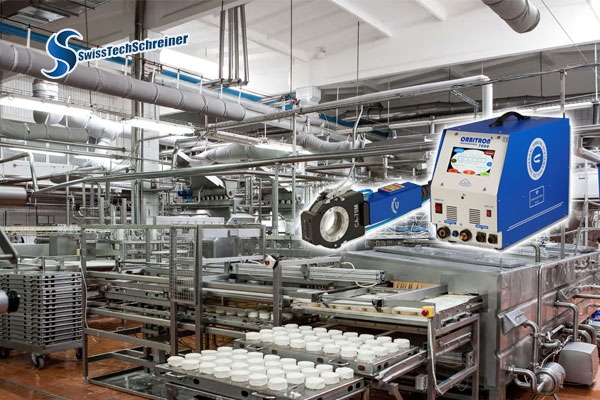
Công nghệ hàn quỹ đạo đảm bảo an toàn thực phẩm
Hãy cùng Swisstech Schreiner tìm hiểu về cách thức vận hành công nghệ hàn quỹ đạo (orbital welding technology) giúp tăng cường hiệu suất sản xuất mà còn đảm bảo chất lượng bề mặt liên kết, giảm thiểu nguy cơ ô nhiễm trong quá trình sản xuất thực phẩm trong các nhà máy thực phẩm qua bài viết sau.
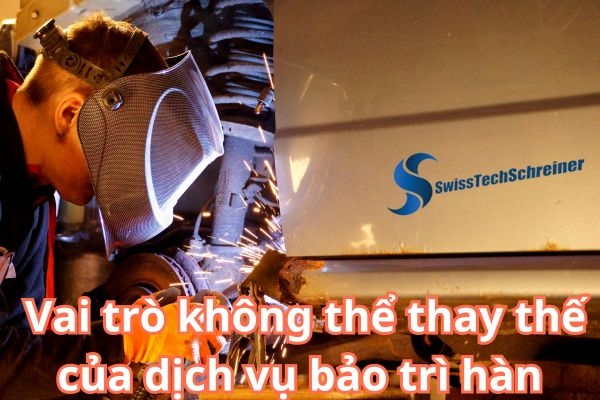
Tăng sức bền cho công trình: Vai trò không thể thay thế của dịch vụ bảo trì hàn - Maintenance work
Các cấu trúc kim loại thường xuyên chịu ảnh hưởng từ tải trọng và điều kiện môi trường khắc nghiệt, khiến chúng dễ bị suy giảm độ bền, phát sinh hiện tượng rạn nứt, oxy hóa hoặc rò rỉ theo thời gian. Nếu không được kiểm tra và bảo trì kịp thời, các vấn đề này có thể gây ra hậu quả nghiêm trọng, ảnh hưởng đến an toàn lao động và vận hành thiết bị.
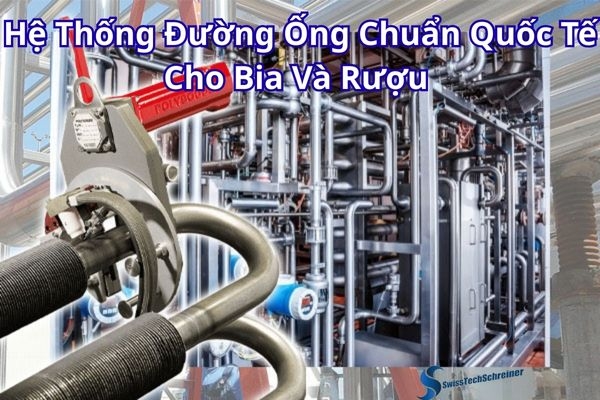
Hệ Thống Đường Ống Chuẩn Quốc Tế Cho Bia Và Rượu - Beverage industry
Việc xây dựng hệ thống đường ống và dây chuyền sản xuất hiện đại, đạt tiêu chuẩn cao là một phần không thể thiếu trong chiến lược phát triển bền vững của các doanh nghiệp trong ngành nước giải khát và bia – rượu. Nhờ ứng dụng công nghệ hiện đại và sự đồng hành của đội ngũ kỹ sư giàu kinh nghiệm